Mirror: http://tinyurl.com/ndt2a6b
वज्र[p= 913,1] a kind of hard mortar or cement (कल्क) VarBr2S. (cf. -लेप) mn. " the hard or mighty one " , a thunderbolt (esp. that of इन्द्र , said to have been formed out of the bones of the ऋषि दधीच or दधीचि [q.v.] , and shaped like a circular discus , or in later times regarded as having the form of two transverse bolts crossing each other thus x ; sometimes also applied to similar weapons used by various gods or superhuman beings , or to any mythical weapon destructive of spells or charms , also to मन्यु , " wrath " RV. or [with अपाम्] to a jet of water AV. &c ; also applied to a thunderbolt in general or to the lightning evolved from the centrifugal energy of the circular thunderbolt of इन्द्र when launched at a foe ; in Northern Buddhist countries it is shaped like a dumb-bell and called Dorje ; » MWB. 201 ; 322 &c ) RV. &c a diamond (thought to be as hard as the thunderbolt or of the same substance with it) , Shad2vBr. Mn. MBh. &c n. a kind of hard iron or steel L. mfn. adamantine , hard , impenetrable W. mfn. shaped like a kind of cross (cf. above ) , forked , zigzag ib. [cf. Zd. vazra , " a club. "](Monier-Williams)
Note: In Rigveda, vajra refers to something hard or mighty compared to a thunderbolt or a jet of water. At what stage of semantic evolution, the gloss was expanded to mean 'adamaentine, glue' is unclear. This is the stage when the artisans might have recognized the feature of cementite, as a nanotube which forms when carbon combines with iron. It is clear that in VarAhamira's time, the gloss vajra meant an adamantine glue: sanghAta. It is possible that this gloss was signified by the sangaDa 'lathe' which is a device most commonly deployed on Indus Script Corpora. Kalyan
The purport of Indus Script corpora is to present metalwork catalogs using hieroglyphs in a writing system deploying rebus-metonymy layered cipher. There are indications that the artisans of Sarasvati-Sindhu (Hindu) civilization worked with ferrous metals based on the rebus readings of the hieroglyph signifiers.
Damaged circular clay furnace, comprising iron slag and tuyeres and other waste materials stuck with its body, exposed at lohsanwa mound, Period II, Malhar, Dist. Chandauli.
Iron artefacts, from the lower and middle levels of Period II, Raja Nala-ka-tila, Dist. Sonbhadra.
Iron artefacts, from the lower and middle levels of Period II, Malhar, Dist. Chandauli.
Highly corroded iron arrowhead, Period I, Dadupur, Dist. Lucknow.
Locations of edarly Iron Age sites: Malhar, Raja Nal-ka Tila,
See: http://bharatkalyan97.blogspot.in/2015/05/rare-discovery-by-prof-kp-rao-of-iron.html Rare discovery by Prof KP Rao of iron tools and weapons in Hyderabad ca. 2200 BCE. This report points to the early date of iron age in Bharatam to ca. 3rd millennium BCE, coterminus with the mature phases of Sarasvati_Sindhu (Hindu) Civilization.
Gregory Possehl and Praveena Gullampalli provide evidence of iron artifacts of Sarasvati-Sindhu (Hindu) Civilization, though there is no evidence of iron smelters in the archaeological sites of the civilization. (Possehl, Gregory L., and Praveena Gullampalli, 1999. The Early Iron Age in South Asia. pp. 153–175 in: Pigott, Vincent C. (ed.), The archaeometallurgy of the Asian Old World. (MASCA Research Papers in Science and Archaeology, University Museum Monograph, volume 16.) Philadelphia: The University Museum, University of Pennsylvania.)
Iron appears in the greater Punjab by 1000 BCE (Possehl & Gullampali, 1999) and earlier in 2nd millennium BCE in eastern N India and Northern Deccan (Hallur, c. 1200 BCE). Atharvaveda has references to metals: 11.3.7 -8 s'yaama ayas (iron), lohita (copper) , trapu (lead), harita (gold) = Paippalada version 16.53.12-13.
See: http://bharatkalyan97.blogspot.in/2011/11/decoding-longest-inscription-of-indus.html Decoding two long inscriptions of Indus Script (Kalyanaraman, 2011)
वज्र[p= 913,1] a kind of hard mortar or cement (कल्क) VarBr2S. (cf. -लेप) mn. " the hard or mighty one " , a thunderbolt (esp. that of इन्द्र , said to have been formed out of the bones of the ऋषि दधीच or दधीचि [q.v.] , and shaped like a circular discus , or in later times regarded as having the form of two transverse bolts crossing each other thus x ; sometimes also applied to similar weapons used by various gods or superhuman beings , or to any mythical weapon destructive of spells or charms , also to मन्यु , " wrath " RV. or [with अपाम्] to a jet of water AV. &c ; also applied to a thunderbolt in general or to the lightning evolved from the centrifugal energy of the circular thunderbolt of इन्द्र when launched at a foe ; in Northern Buddhist countries it is shaped like a dumb-bell and called Dorje ; » MWB. 201 ; 322 &c ) RV. &c a diamond (thought to be as hard as the thunderbolt or of the same substance with it) , Shad2vBr. Mn. MBh. &c n. a kind of hard iron or steel L. mfn. adamantine , hard , impenetrable W. mfn. shaped like a kind of cross (cf. above ) , forked , zigzag ib. [cf. Zd. vazra , " a club. "](Monier-Williams)
Note: In Rigveda, vajra refers to something hard or mighty compared to a thunderbolt or a jet of water. At what stage of semantic evolution, the gloss was expanded to mean 'adamaentine, glue' is unclear. This is the stage when the artisans might have recognized the feature of cementite, as a nanotube which forms when carbon combines with iron. It is clear that in VarAhamira's time, the gloss vajra meant an adamantine glue: sanghAta. It is possible that this gloss was signified by the sangaDa 'lathe' which is a device most commonly deployed on Indus Script Corpora. Kalyan
The purport of Indus Script corpora is to present metalwork catalogs using hieroglyphs in a writing system deploying rebus-metonymy layered cipher. There are indications that the artisans of Sarasvati-Sindhu (Hindu) civilization worked with ferrous metals based on the rebus readings of the hieroglyph signifiers.
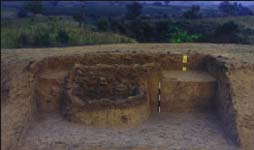
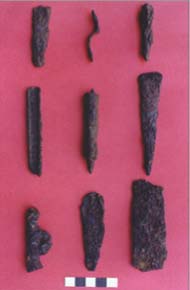
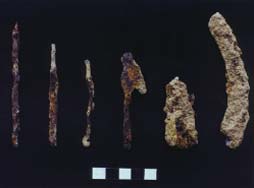
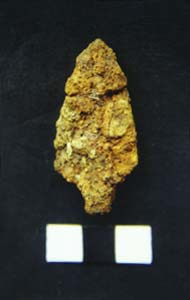
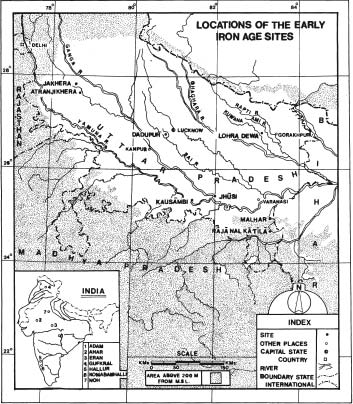
See: http://bharatkalyan97.blogspot.in/2015/05/rare-discovery-by-prof-kp-rao-of-iron.html Rare discovery by Prof KP Rao of iron tools and weapons in Hyderabad ca. 2200 BCE. This report points to the early date of iron age in Bharatam to ca. 3rd millennium BCE, coterminus with the mature phases of Sarasvati_Sindhu (Hindu) Civilization.
Gregory Possehl and Praveena Gullampalli provide evidence of iron artifacts of Sarasvati-Sindhu (Hindu) Civilization, though there is no evidence of iron smelters in the archaeological sites of the civilization. (Possehl, Gregory L., and Praveena Gullampalli, 1999. The Early Iron Age in South Asia. pp. 153–175 in: Pigott, Vincent C. (ed.), The archaeometallurgy of the Asian Old World. (MASCA Research Papers in Science and Archaeology, University Museum Monograph, volume 16.) Philadelphia: The University Museum, University of Pennsylvania.)
Iron appears in the greater Punjab by 1000 BCE (Possehl & Gullampali, 1999) and earlier in 2nd millennium BCE in eastern N India and Northern Deccan (Hallur, c. 1200 BCE). Atharvaveda has references to metals: 11.3.7 -8 s'yaama ayas (iron), lohita (copper) , trapu (lead), harita (gold) = Paippalada version 16.53.12-13.
See: http://bharatkalyan97.blogspot.in/2011/11/decoding-longest-inscription-of-indus.html Decoding two long inscriptions of Indus Script (Kalyanaraman, 2011)
Origins of iron-working in India: Rakesh Tewari (2003). The report is at: http://antiquity.ac....wari/tewari.pdf paged 536-545. This report is significant because recent excavations have produced clear evidence of iron-working at Malhar, Dist. Chandali -- Lat. 24deg.-59'-16"N; Long. 83deg.-15'-46" where a damaged circular clay furnace, comprising iron slag and tuyeres and other waste materials stuck with its body in a stratigraphically dated location. (See Figure 6, page 542). "As discussed elsewhere (Tewari et al. 2000) the sites at Malhar, the Baba Wali Pahari, and the Valley are archaeologically linked to the area of Geruwarwa Pahar which appears to have been a major source of iron ore. The Geruwarwa Pahar situated to the southeast of the Baba Wali Pahari, is full of hematite. Villagers reported (as a tradition passed down from several generations), that the agarias (a particular tribe known for their iron smelting skills) from Robertsganj side, used to come in this area to procure iron by smelting the hematite...The presence of tuyeres, slags, finished iron artefacts, above-mentioned clay structures with burnt internal surface and arms, revealed at Malhar, suggest a large scale activity related to manufacture of iron tools." (p. 542). Malhar is located on river Karamnasa which joins River Ganga at Varanasi. Two radiocarbon dates recorded at this site range around 1800 cal. BCE (Table 2, p. 540) -- precise dates are: 1882 and 2012 BCE. Rakesh Tewari provides the following summary of the evidence from Malhar and other Central Ganga Plain and Eastern Vindhya sites: [Quote]Discussion These results indicate that iron using and iron working was prevalent in the Central Ganga Plain and the Eastern Vindhyas from the early second millennium BC. The dates obtained so far group into three:three dates between c. 1200-900 cal BC, three between c. 1400-1200 cal BC, and five between c. 1800-1500 cal BC. The types and shapes of the associated pottery are comparable to those to be generally considered as the characteristics of the Chalcolithic Period and placed in early to late second millennium BC. Taking all this evidence together it may be concluded that knowledge of iron smelting and manufacturing of iron artefacts was well known in the EasternVindhyas and iron had been in use in the Central Ganga Plain, at least from the early second millennium BC. The quantity and types of iron artefacts, and the level of technical advancement indicate that the introduction of iron working took place even earlier. The beginning of the use of iron has been traditionally associated with the eastward migration of the later Vedic people, who are also considered as an agency which revolutionised material culture particularly in eastern Uttar Pradesh and Bihar (Sharma 1983: 117-131). The new finds and their dates suggest that a fresh review is needed. Further, the evidence corroborates the early use of iron in other areas of the country, and attests that India was indeed an independent centre for the development of the working of iron.[unquote](pp. 543-544).
Thus, both the Gufkral evidence evaluated by Possehl and Gullampalli and the evidence from Malhar and other Central Ganga Plain and Eastern Vindhya sites discussed by Rakesh Tewari point to an indigenous evolution of iron-working in India dated to early 2nd millennium BCE.
The evidence leads to a reasonable hypothesis that the metal-workers of the chalcolithic periods of Sarasvati Civilization moved into the Ganga and Eastern Vindhya iron-age sites to continue the tradition of metal-working, exemplified by the asur-s of Mundarica tradition. No wonder, the Sarasvati hieroglyphs have a significant number of homonyms from the Mundarica tradition to represent metal-working artefacts such as furnaces and minerals used to produce metal products.
The cultural continuity and the indigenous origins of metal-working are areas for further research as excavations proceed on over 2000 Sarasvati River basin sites.
See: http://tinyurl.com/p8qn4bt Meluhha glosses on Indus Script Corpora: bichi (hematite) meḍ ‘iron’ meṛed -bica 'iron stone ore'. Tracing Assur metalworkers into the mists of Bronze Age
1
Santali glosses:...
b
http://www.people.fas.harvard.edu/~witzel/Possehl_Gullampalli.htm
See: https://www.academia.edu/8214398/Indian_iron_and_steel_with_special_reference_to_southern_India_ Sharada Srinivasan, Indian iron and steel, with special reference to southern India (pp.83-90)
D. K. Chakrabarti (1992) argued: "It should be clear that any controversy regarding the meaning of ayas in the Rgveda or the problem of the Rgvedic familiarity or unfamiliarity with iron is pointless. There is no positive evidence either way. It can mean both copper-bronze and iron and, strictly on the basis of the contexts, there is no reason to choose between the two.""The Atharva Veda and the Satapatha Brahmana refer to krsna ayas ("black metal"), which could be iron (but possibly also iron ore and iron items not made of smelted iron). There is also some controversy if the term syamayas ("black metal) refers to iron or not. In later texts the term refers to iron. In earlier texts, it could possibly also refer to darker-than-copper bronze, an alloy of copper and tin...Chakrabarti (1976) has identified six early iron-using centres in India: Baluchistan, the Northwest, the Indo-Gangetic divide and the upper Gangetic valley, eastern India, Malwa and Berar in central India and the megalithic south India.The central Indian region seems to be the earliest iron-using centre. According to Tewari, iron using and iron "was prevalent in the Central Ganga Plain and the Eastern Vindhyas from the early 2nd millennium BC." The earliest evidence for smelted iron in India dates to 1300 to 1000 BCE. These early findings also occur in places like the Deccan and the earliest evidence for smelted iron occurs in Central India, not in north-western India.Moreover, the dates for iron in India are not later than in those of Central Asia, and according to some scholars (e.g. Koshelenko 1986) the dates for smelted iron may actually be earlier in India than in Central Asia and Iran.The Iron Age did however not necessary imply a major social transformation, and Gregory Possehl wrote that 'the Iron Age is more of a continuation of the past then a break with it'...Recent excavations in Middle Ganges Valley conducted by archaeologist Rakesh Tewari show iron working in India may have begun as early as 1800 BCE. Archaeological sites in India, such as Malhar, Dadupur, Raja Nala Ka Tila and Lahuradewa in the state of Uttar Pradesh show iron implements in the period between 1800 BCE-1200 BCE. Sahi (1979: 366) concluded that by the early 13th century BCE, iron smelting was definitely practiced on a bigger scale in India, suggesting that the date the technology's early period may well be placed as early as the 16th century BCE."
https://en.wikipedia.org/wiki/History_of_metallurgy_in_the_Indian_subcontinent
While there is to date no proven evidence for smelted iron in the Indus Valley Civilization, iron ore and iron items have been unearthed in eight Indus Valley sites, some of them dating to before 2600 BCE. (Edwin Bryant (2001). The Quest for the Origins of Vedic Culture: The Indo-Aryan Migration Debate. Oxford University Press, p.339)
Crucible steel and a historic Indian sword of 18th century made of ukku, 'steel' (Telugu) an ancient product of nanotechnology get validated in the context of Indus Script Corpora.
I have demonstrated that all hieroglyphs from Indus Script Corpora and rebus-metonymy Meluhha glosses are relatable to metalwork by ancient Bhāratam Janam.
The monograph discusses, in this context, that the following hieroglyphs are relatable to three categories of ferrous metal: magnetite, hematite and laterite. The findings date the Iron Age of Bhāratam Janam to ca. 3rd millennium BCE.
The Meluhha (mleccha) glosses related to these ferrous minerals are:
poL 'magnetite'; bichi, bicha'hematite'; goTa'laterite'.
The hieroglyphs of Indus Script corpora which signify these ferrous minerals are:
poL 'zebu'; bichi, bicha 'scorpion'; goTa 'something round'.
The hieroglyph which is a glyphic of 'something round' also occurs -- together with composite hieroglyph of trefoil -- on the shawl of the priest-guild-master sculpture, the so-called 'Priest King' of Mohenjo-daro.

Specific ieroglyphs are also relatable to adamantine glue, perhaps cementite of carbon nanotubes recognized in crucible steel ingots from ancient Indian metalworks:
One is sãghāṛɔ 'lathe'.(Gujarati) and another is सांगड [ sāṅgaḍa ] m f (
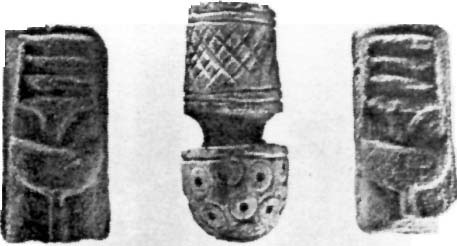
sangaDa 'lathe' (Gujarati) Rebus: sanghAta 'collection, adamentine glue' (Prakritam); jangaDa 'fortification' (Pushto)
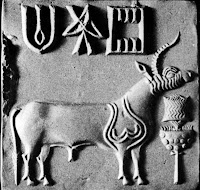


Seal. m1171. Mohenjodaro.Square seal with multiple headed animal depicting three important totemic animals: the bull, the unicorn, and the antelope. All three animals are seen individually on other seals along with script, but this seal has no script.
Material: gray brown steatite
Dimensions: 2.4 x 2.4 cm, 0.53 cm thickness
Mohenjo-daro, DK 7734
Islamabad Museum, NMP 50.289
Mackay 1938: pl. XCVI, 494
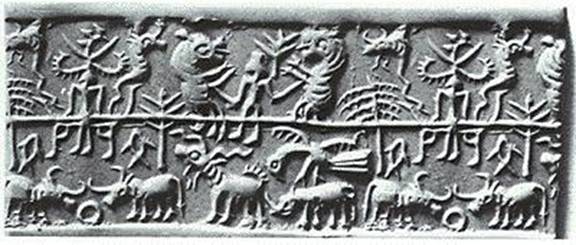
Impression of an Indus-style cylinder seal of unknown Near Eastern origin. Two water-buffalos flanks a hieroglyph: something round, like a seed. Hieroglyph: ranga 'buffalo' Rebus: ranga 'pewter'. What does the hieroglyph 'something round' signify? I suggest that it signifies goTa 'laterite (ferrous ore)'.

This unique mold-made faience tablet or standard (H2000-4483/2342-01) was found in the eroded levels west of the tablet workshop in Trench 54. On one side is a short inscription under a rectangular box filled with 24 dots. The reverse has a narrative scene with two bulls fighting under a thorny tree.
Rebus: gota, laterite.
Hieroglyphs: Ka. gōṭu state of being full-grown, but hard; (also gōṭ-aḍike) a hard, inferior kind of areca-nut. Koḍ. go·ṭ-aḍake full grown, tough areca-nut. Tu. gōṇṭu dried (as the kernel of a coconut), (BRR, also gōṭu) state of being full-grown, dried and hard. Te. goṇṭu-pō̃ka, (B. also) gōṭu-pōka an inferior kind of areca-nut.(DEDR 2202)
(a) Ta. kōṭṭai fort, castle; kōṭu stronghold. Ma. kōṭṭa fort, residence; kōṭu fort. Ko. ko·ṭ castle, palatial mansion. To. kwa·ṭ bungalow. Ka. kōṭe fort, rampart; (PBh.) kōṇṭe fort. Koḍ. ko·ṭe palace. Tu. kōṭè fort. Te. kōṭa, (Inscr.) koṭṭamu id. Kuwi (S.) kōṭa palace, fort. / Cf. Skt. koṭṭa-, koṭa- fort, stronghold. (b) Ko. go·ṛ (obl. go·ṭ-) wall. Ka. gōḍe id. Tu. gōḍè id. Te. gōḍa id. Kol. (SR.) goḍā id. Kuwi (S.) kōḍa wall, prison; (Isr.) kōḍa wall.(DEDR 2207)
*gōṭṭa ʻ something round ʼ. [Cf. guḍá -- 1. -- In sense ʻ fruit, kernel ʼ cert. ← Drav., cf. Tam. koṭṭai ʻ nut, kernel ʼ, Kan. goṟaṭe &c. listed DED 1722]
K. goṭh f., dat. °ṭi f. ʻ chequer or chess or dice board ʼ; S. g̠oṭu m. ʻ large ball of tobacco ready for hookah ʼ, °ṭī f. ʻ small do. ʼ; P. goṭ f. ʻ spool on which gold or silver wire is wound, piece on a chequer board ʼ; N. goṭo ʻ piece ʼ, goṭi ʻ chess piece ʼ; A. goṭ ʻ a fruit, whole piece ʼ, °ṭā ʻ globular, solid ʼ, guṭi ʻ small ball, seed, kernel ʼ; B. goṭā ʻ seed, bean, whole ʼ; Or. goṭā ʻ whole, undivided ʼ, goṭi ʻ small ball, cocoon ʼ, goṭāli ʻ small round piece of chalk ʼ; Bi. goṭā ʻ seed ʼ; Mth. goṭa ʻ numerative particle ʼ; H. goṭ f. ʻ piece (at chess &c.) ʼ; G. goṭ m. ʻ cloud of smoke ʼ, °ṭɔ m. ʻ kernel of coconut, nosegay ʼ, °ṭī f. ʻ lump of silver, clot of blood ʼ, °ṭilɔ m. ʻ hard ball of cloth ʼ; M. goṭā m. ʻ roundish stone ʼ, °ṭī f. ʻ a marble ʼ, goṭuḷā ʻ spherical ʼ; Si. guṭiya ʻ lump, ball ʼ; -- prob. also P. goṭṭā ʻ gold or silver lace ʼ, H. goṭā m. ʻ edging of such ʼ (→ K. goṭa m. ʻ edging of gold braid ʼ, S. goṭo m. ʻ gold or silver lace ʼ); M. goṭ ʻ hem of a garment, metal wristlet ʼ. Ko. gōṭu ʻ silver or gold braid ʼ.(CDIAL 4271)
The gloss used by Meluhha speakers for laterite iron ores is gota.
P. goṭṭā ʻ gold or silver lace ʼ, H. goṭā m. ʻ edging of such ʼ (→ K. goṭa m. ʻ edging of gold braid ʼ, S. goṭo m. ʻ gold or silver lace ʼ); M. goṭ ʻ hem of a garment, metal wristlet ʼ(CDIAL 4271)
Kur. goṭā any seed which forms inside a fruit or shell. Malt. goṭa a seed or berry(DEDR 069) N. goṭo ʻ piece ʼ, goṭi ʻ chess piece ʼ; A. goṭ ʻ a fruit, whole piece ʼ, °ṭā ʻ globular, solid ʼ, guṭi ʻ small ball, seed, kernel ʼ; B. goṭā ʻ seed, bean, whole ʼ; Or. goṭā ʻ whole, undivided ʼ, M. goṭā m. ʻ roundish stone ʼ (CDIAL 4271) <gOTa>(P) {ADJ} ``^whole''. {SX} ``^numeral ^intensive suffix''. *Kh., Sa., Mu., Ho<goTA>,B.<goTa> `undivided'; Kh.<goThaG>(P), Sa.<goTAG>,~<gOTe'j>, Mu.<goTo>; Sad.<goT>, O., Bh.<goTa>; cf.Ju.<goTo> `piece', O.<goTa> `one'. %11811. #11721. <goTa>(BD) {NI} ``the ^whole''. *@. #10971. (Munda etyma)
Rebus: <gota> {N} ``^stone''. @3014. #10171. Note: The stone may be gota, laterite mineral ore stone. khoṭ m. ʻbase, alloyʼ (Punjabi) Rebus: koṭe ‘forging (metal)(Mu.) Rebus: goṭī f. ʻlump of silver' (G.) goṭi = silver (G.) koḍ ‘workshop’ (Gujarati).
पोळ [ pōḷa ] m A bull dedicated to the gods, marked with a trident and discus, and set at large.
Hump
पोळी [ pōḷī ] dewlap. Rebus: Russian gloss, bulat is cognate pola 'magnetite' iron in Asuri (Meluhha). Magnetite is the most magnetic of all the naturally occurring igneous and metamorphic rocks with black or brownish-black with a metallic luster. These magnetite ore stones could have been identified as pola iron by Meluhha speakers. Kannada gloss pola meaning 'point of the compass' may link with the characteristic of magnetite iron used to create a compass.pŏlāduwu made of steel; pŏlād प्वलाद् or phōlād फोलाद् मृदुलोहविशेषः ] m. steel (Gr.M.; Rām. 431, 635, phōlād). pŏlödi pōlödi phōlödi लोहविशेषमयः
adj. c.g. of steel, steel (Kashmiri) urukku what is melted, fused metal, steel.(Malayalam); ukk 'steel' (Telugu)(DEDR 661) This is cognate with famed 'wootz'steel. "Polad, Faulad" for steel in late Indian languages is traceable to Pokkhalavat, Polahvad. Pokkhalavat is the name of Pushkalavati, capital of Gandhara famed for iron and steel products.
Allograph: పొల [ pola ] or పొలసు pola. పొలుసు [ polusu ][Telugu] A scale of a fish. చేపమీది పొలుసు. Tu. poḍasů scales of fish. Te. pola, polasu, polusu id. Kui plōkosi id. (DEDR 4480). పొలుపు [ polupu ] or పొల్పు polupu. [Telugu] Firmness,స్థైర్యము. "పొలుపుమీరిన నెలవంకిబొమలు జూచి, రమణదళుకొత్తు బింబాధరంబుజూచి." Rukmang. i. 158
H. muḍḍhā m. ʻ shoulder ʼ, mū̃ḍhā m. ʻ lump, hump, shoulder ʼ Or. muṇḍā ʻ lump ʼ.(CDIAL 10189) Rebus: muṇḍa ‘iron’ (Sanskrit) mRdu, 'soft', kuṇṭha, 'hard', kadāra 'brittle' are three varieties of muṇḍa loha(Vagbhata,
Rasaratnasamuccaya, 69-74). muṇḍitam, muṇḍa loham 'iron'; muṇḍajam 'steel' (Sanskrit) Thus, zebu reads rebus: kuṇṭha munda (loha), a type of iron native metal. (Vagbhata, Rasaratnasamuccaya, 69-74).
pola (magnetite), gota (laterite), bichi (hematite).
Seal. Lothal 51
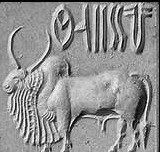
A type of hard native metal, ferrous oxide – kuṇṭha munda (loha) is denoted by khũṭ 'zebu'/ mū̃ḍhā 'hump' hieroglyphs.
goṭi, ‘silver, laterite’ are denoted by goṭa, ‘seed’ hieroglyph.

bichi , ‘hematite’ is denoted by hieroglyph bicha ‘scorpion’ (Assamese) Rebus: bica ‘stone ore’ (Santali).
Cylinder seal; BM 122947; U. 16220; humped bull stands before a palm-tree, feeding froun a round manger or a bundle of fodder; behind the bull is a scorpion and two snakes; above the whole a human figure, placed horizontally, with fantastically long arms and legs, and rays about his head.
Hieroglyph: Bi. mẽṛhwā ʻ a bullock with curved horns like a ram's ʼ; M. mẽḍhrū̃ n. ʻ sheep ʼ.(CDIAL 10311) mēṇḍha2 m. ʻ ram ʼ, °aka -- , mēṇḍa -- 4, miṇḍha -- 2, °aka -- , mēṭha -- 2,mēṇḍhra -- , mēḍhra -- 2, °aka -- m. lex. 2. *mēṇṭha- (mēṭha -- m. lex.). 3. *mējjha -- . [r-- forms (which are not attested in NIA.) are due to further sanskritization of a loan -- word prob. of Austro -- as. origin (EWA ii 682 with lit.) and perh. related to the group s.v. bhēḍra -- ] Pa. meṇḍa -- m. ʻ ram ʼ, °aka -- ʻ made of a ram's horn (e.g. a bow) ʼ; Pk. meḍḍha -- ,meṁḍha -- (°ḍhī -- f.), °ṁḍa -- , miṁḍha -- (°dhiā -- f.), °aga -- m. ʻ ram ʼ, Dm. Gaw. miṇKal.rumb. amŕn/aŕə ʻ sheep ʼ (a -- ?); Bshk. mināˊl ʻ ram ʼ; Tor. miṇḍ ʻ ram ʼ, miṇḍāˊl ʻ markhor ʼ; Chil. mindh*ll ʻ ram ʼ AO xviii 244 (dh!), Sv. yēṛo -- miṇ; Phal. miṇḍ, miṇ ʻ ram ʼ,miṇḍṓl m. ʻ yearling lamb, gimmer ʼ; P. mẽḍhā m., °ḍhī f., ludh. mīḍḍhā, mī˜ḍhā m.; N. meṛho,meṛo ʻ ram for sacrifice ʼ; A. mersāg ʻ ram ʼ ( -- sāg < *chāgya -- ?), B. meṛā m., °ṛi f., Or.meṇḍhā, °ḍā m., °ḍhi f.,H. meṛh, meṛhā, mẽḍhā m., G. mẽḍhɔ, M. mẽḍhā m., Si. mäḍayā.2. Pk. meṁṭhī -- f. ʻ sheep ʼ; H. meṭhā m. ʻ ram ʼ.3. H. mejhukā m. ʻ ram ʼ.(CDIAL 10310) <menDa>(A) {N} ``^sheep''. *Des.<meNDa>(GM) `sheep'. #21810<meD>(:) <arij=meD>(Z),,<ari?=me?n>(A) {N} ``^female ^kid''. ^goat. #3022.<kin=meD>(Z) {N} ``^male ^goat, billy goat''. |<kin> `prefix used in names of male animals'. #17072. <auG kinme?n>(A) {N} ``^nanny ^goat''. |<auG> `mother'. #3729.(Gorum)![]()
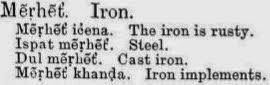
Sa. <i>mE~R~hE~'d</i> `iron'. ! <i>mE~RhE~d</i>(M).
Ma. <i>mErhE'd</i> `iron'.
Mu. <i>mERE'd</i> `iron'.
~ <i>mE~R~E~'d</i> `iron'. ! <i>mENhEd</i>(M).
Ho <i>meD</i> `iron'.
Bj. <i>merhd</i>(Hunter) `iron'.
KW <i>mENhEd</i>
@(V168,M080)
— Slavic glosses for 'copper'
Мед [Med]Bulgarian
Bakar Bosnian
Медзь [medz']Belarusian
Měď Czech
Bakar Croatian
KòperKashubian
Бакар [Bakar]Macedonian
Miedź Polish
Медь [Med']Russian
Meď Slovak
BakerSlovenian
Бакар [Bakar]Serbian
Мідь [mid'] Ukrainian[unquote]
Miedź, med' (Northern Slavic, Altaic) 'copper'.
One suggestion is that corruptions from the German "Schmied", "Geschmeide" = jewelry. Schmied, a smith (of tin, gold, silver, or other metal)(German) result in med ‘copper’.
Hieroglyph of a worshipper kneeling: Konḍa (BB) meḍa, meṇḍa id. Pe. menḍa id.
Manḍ. menḍe id. Kui menḍa id. Kuwi (F.) menda, (S. Su. P.) menḍa, (Isr.) meṇḍa id.
Ta. maṇṭi kneeling, kneeling on one knee as an archer. Ma.maṇṭuka to be seated on the heels. Ka. maṇḍi what is bent, the knee. Tu. maṇḍi knee. Te. maṇḍĭ̄ kneeling on one knee. Pa.maḍtel knee; maḍi kuḍtel kneeling position. Go. (L.) meṇḍā, (G. Mu. Ma.) Cf. 4645 Ta.maṭaṅku (maṇi-forms). / ? Cf. Skt. maṇḍūkī- (DEDR 4677)
See: http://bharatkalyan97.blogspot.in/2014/09/catalogs-of-pola-kuntha-gota-bichi.html
Catalogs of pola, kuṇṭha, goṭa, bichi native metalwork in Meluhha Indus script hieroglyphs


Hematite ore, Michigan.
Wootz was extracted from raw iron ore (hematite) and formed as steel using a crucible to melt, burn away impurities and adding ingredients (i.e., high carbon content of 1.5% by weight); this was made in southern and central India and Sri Lanka ca. 300 BCE. High carbon content results in the sharpness of the edge and durability. Too little carbon results in wrought iron and too much carbon results in cast iron.
a. Damascus sword; b. Wavy pattern on the sword.
HRTEM images of remnants from dissolution of a sample of genuine Damascus sabre in hydrochloric acid. a,b. MWCNTs with the characteristic distance of d = 0.34 nm. In b, the tubes are bent like a rope. c. Remnants of cementite nanowires encapsulated by CNTs, which prevent wires from dissolving in acid. Scale bars: 5 nm (a) and (c) and 10 nm (b) Reproduced from Reibold et al with permission from P. Paufler.
In carbon steels and cast irons that are slowly cooled a portion of the elements is in the form of cementite. Cementite, also known as iron carbide, is a chemical compound of iron and carbon, with the formula Fe3C. It is a hard and brittle material, essentially a ceramic. Cementite appears as crystallized forms (called nanotubes or nanowire structure) in Damascus (Indian crucible steel) swords.

Analysis of the nanotube structure of Damascus steel. The swords forged in Damascus had a surface pattern of moiré ripples, which resemble turbulent water, with a wavy pattern on its surface which looks like wood grain. Details: (a). A Damascus sword; (b). the wavy pattern in the sword; (c-d). the nanowire structure of the steel in the blade. (Source: C. Srinivasan, Damascus Sword - An Ancient Product of Nanotechnology).
See: http://bharatkalyan97.blogspot.in/2015/02/vajra-sanghata-binding-together.html
A possible reference to the properties of cementite occurs in VarAhamihira's Brhatsamhita which uses the phrase:
Vajra Sanghāta 'binding together': Hieroglyph: sãghāṛɔ 'lathe'.(Gujarati). Purport of Indus Script corpora. Vajra Sanghāta 'binding together': Mixture of 8 lead, 2 bell-metal, 1 iron rust constitute adamantine glue.
In Indus Script Corpora, the gloss sanghāta 'binding together' is signified by the hieroglyph: sãghāṛɔ 'lathe'. (Gujarati). It is possible that the gloss sanghāta was meant to refer to alloys of minerals and formation of cementite such as Vajra Sanghāta on metal crystalline formations.
The samasa used by Varahamihira is Vajra sanghāta, an adamantine glue. In this context, the meaning of the word is: 'alloying, mixing, binding together' (to achieve metallic cementing.
I am grateful to Prof. Subbarayappa Bidare for leading me to this citation from Varahamira and presenting the context of metallic cementing.
VarAhamihira's Brhatsamhita explains Vajra sanghAta as Mixture of 8 lead, 2 bell-metal, 1 iron rust constitute adamantine glueThe samasa used by Varahamihira is vajrasanghAta, an adamantine glue.
The proportions of metals mentioned makes the use of the word sanghAta a rebus reading of the hieroglyph: sanghADo 'lathe' (Gujarati). Given the emphatic evidence of almost ALL pictorial motifs and signs of the Indus Script are related to metalwork, it is apposite to treat the gloss sanghAta as related to a metal alloy.
In the context of SanghATa Sutra dharma paryAya, the narration by Shakyamuni (Gautama) is related to the combinations constituting the cumulative, knowledge of dharma (arrived by churning in thought). So, sangADo 'lathe' is evocative of circular churning motion to drill or perforate; while the homonym, sanghAta as indicated by Varahamiri may connote a 'mixing or combination (of metals)', as a second meaning. First meaning is: sanghAta 'collection of words (reading hieroglyphs as words)'; the second meaning is: 'collection of materials (indicated by hieroglyphs read as words)'.
The samasa used by Varahamihira is Vajra sanghāta, an adamantine glue. In this context, the meaning of the word is: 'alloying, mixing, binding together' (to achieve metallic cementing.
I am grateful to Prof. Subbarayappa Bidare for leading me to this citation from Varahamira and presenting the context of metallic cementing.
"Wootz was produced from carburisation of wrought iron which was heated in closed crucibles with dry wood chips, stems and leaves of plants over charcoal fire maintained by blowing air with large bellows. The operation took 4-5 hours to complete. Steels so obtained was heated again so that the excess carbon was burnt off...This gives credence to the use of crucible process in early periods, as Ray believes, that this process was the continuation of the original process which was acquired by the ancient smiths even before the beginning of the Common era....Prakash has also quoted from Rasaratnasamucchaya which gives a detailed description of composition of a crucible and of classifications of iron and steel." [Bhatia, SK, 1994, Carburisation of iron in Ancient India, in: Indian Journal of History of Science, 29(3), pp.353-359].
"The iron...produced was classified into two main categories, viz., (i) wrought iron (kAntalohA) and (ii) carbon steel (tIkshNalohA) and the third category was (iii) cast iron (MundalohA0 which was considered undesirable till its refining technique was developed to convert it into 'wootz' steel..."(p.354) "VarAhamihira (c. 550 CE) has mentioned the following processes for carburizing and hardening of iron swords: (i) making a paste with the juice of the plant arka (calotropis gigantea), the gelatin from the sheep's horn and pigeon's and mouse dung, applying this paste to the steel after rubbing it with sesame oil, heating the swod in the fire and when it is red hot sprinkling on it water or mil of mares (camel or goat) or ghee (clarified butter) or blood or fat or bile and then sharpening on the lathe; (ii) plunging the steel red hot into a solution of plantain ashes in whey, keeping it standing for twenty four hours, and then sharpening on the lathe (VarAhamihira Khargalakshanam, Chap. XVIX, Slokas 23-26)...Wootz...The first process consisted of carburization of soft iron or wrought iron by packing it with chips of wood and leaves of specific plants, e.g. avaram (cassia auriculata), etc. about 1/10th in weight of the iron and then the mouth of the crucible was sealed with clay...In the second process of steel making, a pool of highly oxidizing molten slag was prepared from magnetite sand and quartz which has a melting point of 1205 degrees C and it was used for refining cast iron by oxidation of carbon and other impurities. For this process, a specially designed compartmentalised pit furnace was made below the ground level and cast iron (rejected from the bloomery furnace) was added in the molten oxidizing slag in the form of red hot small shots. During the process of steel making, the surface of the cast iron reacted with FeO to decarbonise and dephosphorise the iron which became molten steel and got collected at the bottom..."(p.360-363) "VarAhamihira has mentioned that the hardening of the sword was done by plunging it in whey in a mixture of water and plantain ashed or oil. Another way of achieving the hard edge on the sword was to run fast on a horse holding the red hot sword with its sharp edge in the front. The typical hardening treatment was given by quenching the red hot high carbon steel in water or oil for a few seconds and then withdrawing to observe as the tempering was achieved due to the flow of heat from the body of the tool... "(p.369)(Prakash, B., 1991, Metallurgy of iron and steel making and blacksmithy in ancient India, IJHS, Vol. 26, No. 4, pp. 351-371) http://www.new1.dli.ernet.in/data1/upload/insa/INSA_1/20005ac0_351.pdf
"Swords made of crucible steel have also been excavated from 3rd-4th century CE burials in the Russian Northern Caucasus. One of these blades has aligned spheroidal cementite, the metallograhic feature that produces the visible pattern. This is the earliest known crucible Damascus blade." (Ann Feuerbach, Crucible Damascus steel: a fascination for almost 2000 years in JOM, May 2006).
https://www.academia.edu/397355/Crucible_Damascus_Steel_A_Fascination_for_Almost_2_000_Years
An iron smelting furnace of the Agarias. http://www.dli.gov.in/rawdataupload/upload/insa/INSA_1/20005afd_33.pdf
http://www.ias.ac.in/resonance/Volumes/11/06/0067-0077.pdf A tale of wootz steel by S. Ranganathan and Sharada Srinivasan in: Resonance, June, 2006
See: S. Ranganathan and Sharada Srinivasan:
1. http://www.sanskritimagazine.com/history/tale-crucible-wootz-steel-ancient-india/ A tale of crucible (wootz) steel from Ancient India
2. http://greaterancestors.com/steel-from-ancient-india-wootz-steel/ Steel from Ancient India (Wootz steel): An advanced material of the ancient world
Mirror: http://materials.iisc.ernet.in/~wootz/heritage/WOOTZ.htm
https://www.scribd.com/doc/268638164/Metallurgy-of-Iron-and-Steel-Making-and-Blacksmithy-in-Ancient-India-B-Prakash-1991

High-quality steel has been produced in South India since ancient times. The technique used to manufacture it was later on called the crucible technique. Pure wrought iron was first put together with glass and charcoal in a container and was heated till the metal melted and absorbed the carbon. http://www.mazhalaigal.com/gk/inventors/201210nbs_indian-inventions.php

Crucibles next to the furnace room at Abbeydale, Sheffield. The shapes of the crucibles compare with those found in India.
Nanotubes are said to explain the sword's sharpness.
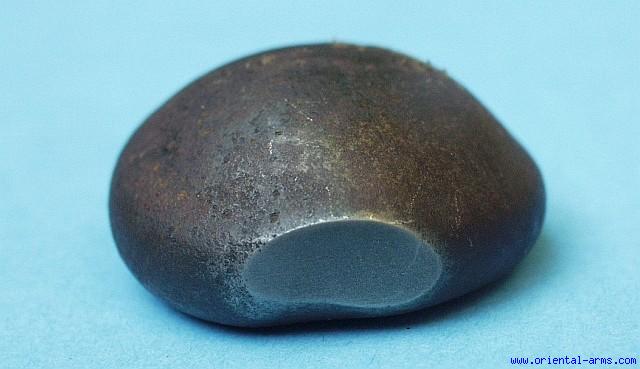
Real 18 c. Wootz (Damascus) Steel Ingot right out of the crucible and ready to be forged. http://www.oriental-arms.co.il/item.php?id=1411
Historic Indian sword was masterfully crafted
Italian, UK researchers use non-destructive techniques and show the secrets of forging methods
New York | Heidelberg, 10 February 2015
The master craftsmanship behind Indian swords was highlighted when scientists and conservationists from Italy and the UK joined forces to study a curved single-edged sword called a shamsheer. The study, led by Eliza Barzagli of the Institute for Complex Systems and the University of Florence in Italy, is published in Springer’s journal Applied Physics A - Materials Science & Processing.
The 75-centimeter-long sword from the Wallace Collection in London was made in India in the late eighteenth or early nineteenth century. The design is of Persian origin, from where it spread across Asia and eventually gave rise to a family of similar weapons called scimitars being forged in various Southeast Asian countries.
Two different approaches were used to examine the shamsheer: the classical one (metallography) and a non-destructive technique (neutron diffraction). This allowed the researchers to test the differences and complementarities of the two techniques.
The sword in question first underwent metallographic tests at the laboratories of the Wallace Collection to ascertain its composition. Samples to be viewed under the microscope were collected from already damaged sections of the weapon. The sword was then sent to the ISIS pulsed spallation neutron source at the Rutherford Appleton Laboratory in the UK. Two non-invasive neutron diffraction techniques not damaging to artefacts were used to further shed light on the processes and materials behind its forging.
“Ancient objects are scarce, and the most interesting ones are usually in an excellent state of conservation. Because it is unthinkable to apply techniques with a destructive approach, neutron diffraction techniques provide an ideal solution to characterize archaeological specimens made from metal when we cannot or do not want to sample the object,” said Barzagli, explaining why different methods were used.
It was established that the steel used is quite pure. Its high carbon content of at least one percent shows it is made of wootz steel. This type of crucible steel was historically used in India and Central Asia to make high-quality swords and other prestige objects. Its band-like pattern is caused when a mixture of iron and carbon crystalizes into cementite. This forms when craftsmen allow cast pieces of metal (called ingots) to cool down very slowly, before being forged carefully at low temperatures. Barzagli’s team reckons that the craftsman of this particular sword allowed the blade to cool in the air, rather than plunging it into a liquid of some sort. Results explaining the item’s composition also lead the researchers to presume that the particular sword was probably used in battle.
Craftsmen often enhanced the characteristic “watered silk” pattern of wootz steel by doing micro-etching on the surface. Barzagli explains that through overcleaning some of these original ‘watered’ surfaces have since been obscured, or removed entirely. “A non-destructive method able to identify which of the shiny surface blades are actually of wootz steel is very welcome from a conservative point of view,” she added.
Reference: Barzagli E. et al (2015). Characterization of an Indian sword: classic and noninvasive methods of investigation in comparison, Applied Physics A - Materials Science & Processing. DOI 10.1007/s00339-014-8968-0
Credit: Dr. Alan Williams/Wallace Collection
Revealed: Secrets of craftsmanship behind ancient Indian sword (Single-edged called Shamsheer)
- Vanita Srivastava, Hindustan Times, New Delhi |
- Updated: Feb 12, 2015 16:39 IST
The 75-cm ‘shamsheer’ was made in India in the late 18th or early 19th century. (Photo: Dr Alan Williams/Wallace Collection, London)
The master craftsmanship behind Indian swords was highlighted when scientists and conservationists from Italy and the UK joined forces to study a curved single-edged sword called shamsheer.
The study, led by Eliza Barzagli of the Institute for Complex Systems and the University of Florence in Italy, is published in Springer’s journal Applied Physics A-Materials Science & Processing.
The 75-cm sword from the Wallace Collection in London was made in India in the late eighteenth or early nineteenth century. The design is of Persian origin, from where it spread across Asia and eventually gave rise to a family of similar weapons, called scimitars, forged in various Southeast Asian countries.
Two different approaches were used to examine the shamsheer — metallography and a non-destructive technique, neutron diffraction — allowing researchers to test the differences and complementarities of the techniques.
“Ancient objects are scarce. The most interesting ones are usually in an excellent state of conservation. Because it is unthinkable to apply techniques with a destructive approach, neutron diffraction techniques provide an ideal solution to characterise archaeological specimens made from metal when we cannot or do not want to sample the object,” said Barzagli.
The sword’s high carbon content — of at least one percent — shows it is made of wootz steel. This type of crucible steel was historically used in India and Central Asia to make high-quality swords and other prestige objects. Its band-like pattern is caused when a mixture of iron and carbon crystalises into cementite. This forms when craftsmen allow cast pieces of metal to cool down slowly, before being forged at low temperatures.http://www.hindustantimes.com/india-news/secrets-of-ancient-indian-sword-revealed/article1-1315957.aspx
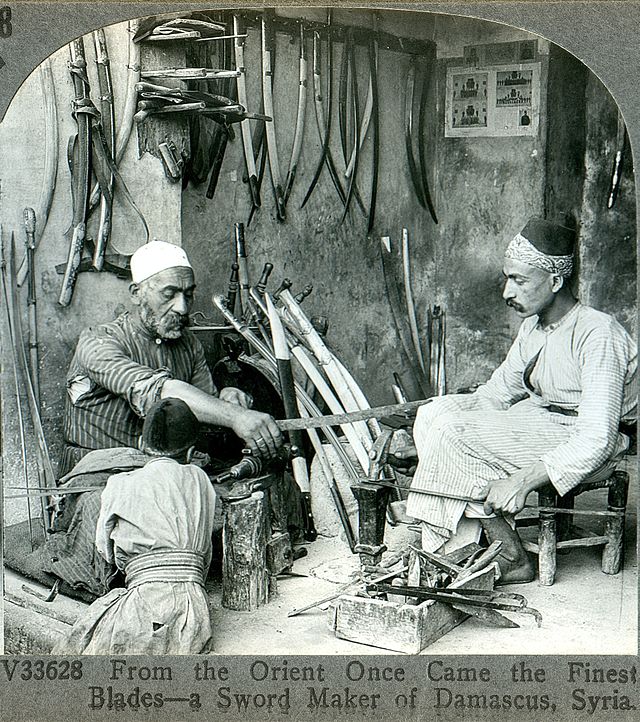
A sword maker from damascus, ca. 1900
A carbide-banding phenomenon produced by the microsegregation of minor amounts of carbide-forming elements present in the wootz ingots aid the process of forging Damascus sabre blade with sharp edges.
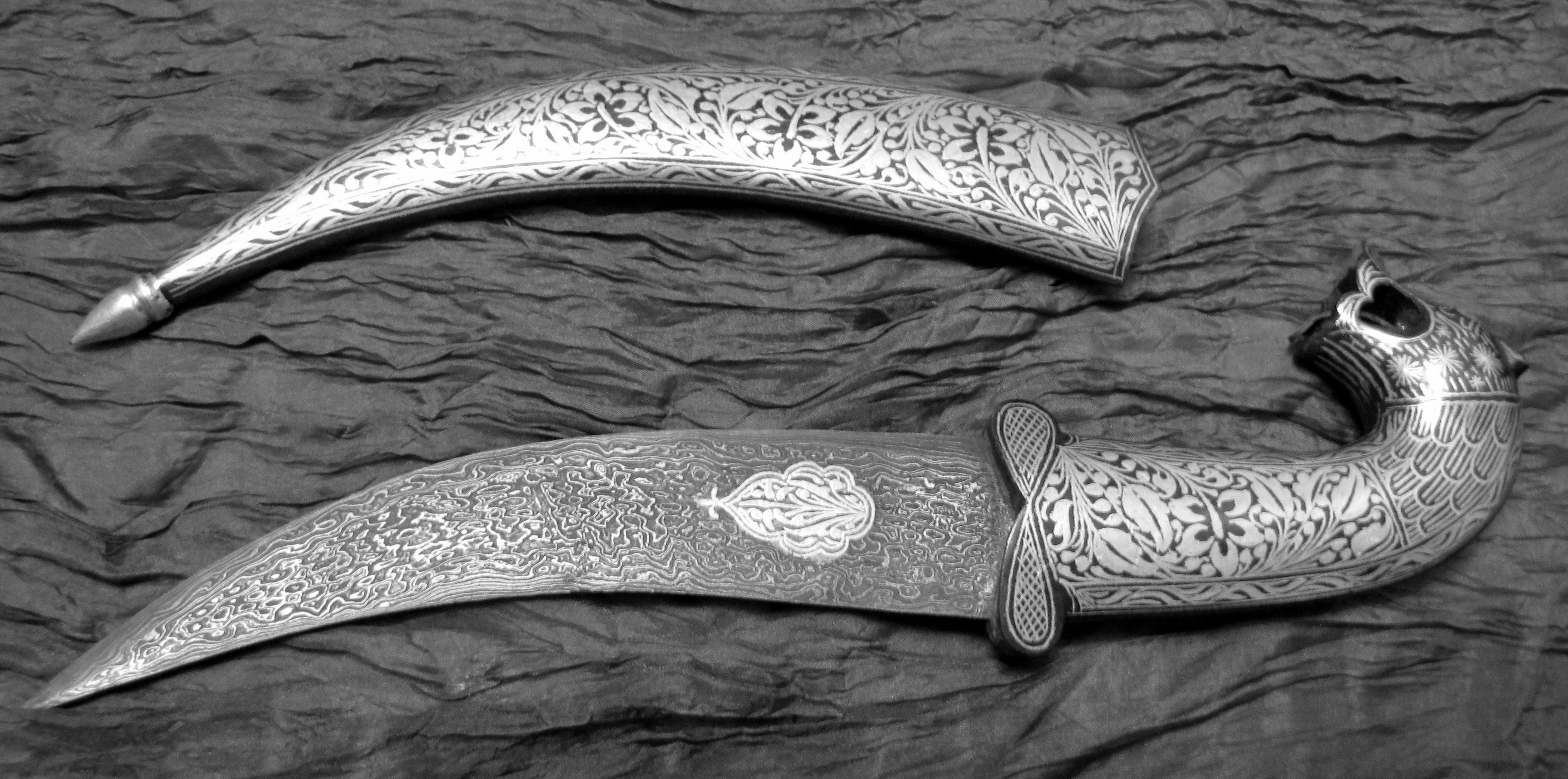
A beautiful example of a Damascus steel knife. Notice the dark patterns—similar to both soot and the cave paintings. https://www.flickr.com/photos/jasleen_kaur/4211340481/

http://link.springer.com/article/10.1007%2Fs11837-998-0419-y#page-1 Verhoeven, JD, AH Pendray, WE Dauksch, The key role of impurities in ancient damascus steel blades in: JOM, 1998, Vol. 50, Issue 9, pp. 58-64.
Crucible steel samples from Bharatam which result in Damascus swords are the earliest carbon nanotubes on record. The carbon nanotubes might have contributed to the formation of iron carbide nanowires.
Reference https://www.physicsforums.com/threads/damascus-steel-and-carbon-nanotubes.144911/
Boukhvalov, DW, MI Katsnelson, Yu.N. Gornostyrev in: Effect of impurities on growth and morphology of cementite nanowires. The authors examined the role of several realistic impurities (Si, Mn, V, P and S) in the formation energies of the cementite nanowires with different sizes and morphologies. It is shown that the presence of the impurities decreases the formation energy and can switch the preferable axis of the cementite nanowire growth. http://arxiv.org/ftp/arxiv/papers/1201/1201.5327.pdf
Nature 444, 286 (16 November 2006) | doi:10.1038/444286a; Received 24 July 2006; Accepted 25 October 2006; Published online 15 November 2006
Materials: Carbon nanotubes in an ancient Damascus sabre
Top
![Sabre #10, Berne Historical Museum, Switzerland, Assad Ullah in the 17th Century. - Peter Paufler (c) 2006]()
Srinivasan, C., Do Damascus swords reveal India's mastery of nanotechnology? in: Current Science, Vol. 92, No. 3, 10 February 2007, pp. 279-280
![]()
Carbon nanotubes
Carbon nanotubes are long chains of carbon held together by the strongest bond in all chemistry, the sacred sp2 bond, even stronger than the sp3 bonds that hold together diamond. Carbon nanotubes have numerous remarkable physical properties, including ballistic electron transport (making them ideal for electronics) and so much tensile strength that they are the only substance that could be used to build a space elevator. The specific strength of carbon nanotubes is 48,000 kN·m/kg, the best of known materials, compared to high-carbon steel’s 154 kN·/kg. That’s 300 times stronger than steel. You could build towers hundreds of kilometers high with it.
From Arab Seafaring by George F. Hourani:
http://www.muslimheritage.com/article/filling-gap-history-pre-modern-industry-1000-years-missing-islamic-industry
By Rakesh Tewari
Recent excavations in Uttar Pradesh have turned up iron artefacts, furnaces, tuyeres and slag in layers radiocarbon dated between c. BCE 1800 and 1000. This raises again the question of whether iron working was brought in to India during supposed immigrations of the second millennium BCE, or developed independently.
![table]()
* These dates are calibrated by Dr B. Sekar, BSIP, Lucknow. References for datasets used: Stuiver, et al. 1998a. 537![map]()
Painted black-and-red ware shards, from early iron bearing deposits of Period II, Raja Nala-ka-tila, Dist. Sonbhadra.
Iron artefacts, from the lower and middle levels of Period II, Raja Nala-ka-tila, Dist. Sonbhadra.
Table 2. New 14C dates for early iron-use from the Ganga Plain and the Eastern Vindhyas
![table]()
* These dates are calibrated by Dr B. Sekar, BSIP, Lucknow. References for datasets used: Stuiver, et al. 1998a.
Iron artefacts, from the lower and middle levels of Period II, Malhar, Dist. Chandauli.
![Naugarh kot iron]()
Damaged circular clay furnace, comprising iron slag and tuyeres and other waste materials stuck with its body, exposed at lohsanwa mound, Period II, Malhar, Dist. Chandauli.
Highly corroded iron arrowhead, Period I, Dadupur, Dist. Lucknow.
Abstract
The steel of Damascus blades, which were first encountered by the Crusaders when fighting against Muslims, had features not found in European steels — a characteristic wavy banding pattern known as damask, extraordinary mechanical properties, and an exceptionally sharp cutting edge. Here we use high-resolution transmission electron microscopy to examine a sample of Damascus sabre steel from the seventeenth century and find that it contains carbon nanotubes as well as cementite nanowires. This microstructure may offer insight into the beautiful banding pattern of the ultrahigh-carbon steel created from an ancient recipe that was lost long ago.
"Damascus blades featured two qualities not found in European steels at that time: an attractive wavy-like banding, known today as Damast, an extremely sharp edge (according to the legend a sword could slice through a silk handkerchief floating in the air)...The formation of the (Damast) pattern depends on the formation of cementite (Fe3C) particles of a certain size, shape and spatial distribution...How was genuine Damascus steel done? It is generally agreed that those ingots of crucible steel were made in ancient India ('wootz') and Central Asia ('bulad'), then sold to the Near East and to Europe for forging. Details of the blade production were kept secret. At the end of the 18th century the ability to produce this type of steel got lost. Numerous attempts have been made since that time to reproduce this quality...a pronounced structuring of the material at nanoscale has been observed. One component of this is the appearance of wire-like objects of cementite structure...Their spacing is of the order of 100nm...Taking ancient recipes of wootz-technology into account, we have speculated that organic additions with the aid of catalysts might have given rise to this carbon nanotube formation..."
Fig. 1. Transmission Electron Microscopy (TEM) image of cementite nanowires in a Damascus sabre. Left panel: The dark stripes indicate wires of several nanometers in length. Right panel: View showing an almost circular fross section (dotted)
Legendary Swords' Sharpness, Strength From Nanotubes, Study Says
Mason Inman
for National Geographic News
for National Geographic News
November 16, 2006
New studies of Damascus swords are revealing that the legendary blades contain nanowires, carbon nanotubes, and other extremely small, intricate structures that might explain their unique features.
Damascus swords, first made in the eighth century A.D., are renowned for their complex surface patterns and sharpness. According to legend, the blades can cut a piece of silk in half as it falls to the ground and maintain their edge after cleaving through stone, metal, or even other swords.
But since the techniques for making these swords have been lost for hundreds of years, no one is sure exactly why these swords are so exceptional.
Now studies of the swords' molecular structure are uncovering the tiny structures that may explain these properties.
Peter Paufler, a crystallographer at Technical University in Dresden, Germany, and his colleagues had previously found tiny nanowires and nanotubes when they used an electron microscope to examine samples from a Damascus blade made in the 17th century.
Today in the journal Nature, the teams reports that it has also discovered carbon nanotubes in the sword—the first nanotubes ever found in steel, Paufler says.
The nanotubes, which are remarkably strong, run through the blade's softer steel, likely making it more resilient. (Related: "Nano-Switches Could Yield Even Smaller Gadgets"[August 16, 2005].)
"It is a general principle of nature," Paufler said. "Materials that are softer, you can strengthen by including harder wires."
Secret Techniques
Some of the nanowires Paufler and his team had previously found were made of an extremely hard iron-based mineral called cementite.
In the new research, the team discovered that carbon nanotubes encase some cementite nanowires, protecting them.
These nanotube-nanowire bundles may give the swords their special properties, Paufler says.
The bundles run parallel to the blade's surface and may help larger particles of cementite arrange in layers. These hard layers, which have softer steel in between, could help explain how the steel remains strong yet flexible.
This combination of strength and flexibility makes the steel ideal for forging swords.
The blades were generally made from metal ingots prepared in India using special recipes, which probably put just the right amount of carbon and other impurities into the iron (India map).
By following these recipes and following specific forging techniques, "craftsmen ended up making nanotubes more than 400 years ago," Paufler and his colleagues write.
When these blades were nearly finished, blacksmiths would etch them with acid. This brought out the wavy light and dark lines that make Damascus swords easy to recognize.
But it could also give the swords their sharpness, Paufler says. Because carbon nanotubes are resistant to acid, they would protect the nanowires, he theorizes.
After etching, many of these nanostructures could stick out from the blade's edge, giving it tiny saw-like teeth.
Skeptical Smiths
The techniques for making the steel were lost around A.D. 1700. But many researchers are studying how to recreate the blades—even though metallurgical experts warn that the blades, though exceptional for their time, are far outperformed by modern steels.
While some scientists have claimed success, others dispute that the reproductions are truly the same as the originals.
And many experts doubt that the new findings will clear things up.
John Verhoeven, a metallurgist at Iowa State University at Ames who has worked on reproducing the Damascus sword-making techniques, is skeptical that Paufler and his colleagues have cracked the secret of Damascus blades.
"I don't think that [the nanowires] are anything unusual," Verhoeven said. "I think those structures would be found in normal steels."
The Damascus sword is also an example of how unexpected nanosize structures can show up in materials—and sometimes give them surprising properties, experts say.
But not all these nanoproperties are good. Asbestos, for example, comes in needle-like particles that cause severe lung disease. Break these particles into shorter pieces, and they much less harmful.
Because of nanomaterials' unpredictable behavior, several researchers asked in an article published today in Nature for more studies of these materials and their potential side effects.
Srinivasan, C., Do Damascus swords reveal India's mastery of nanotechnology? in: Current Science, Vol. 92, No. 3, 10 February 2007, pp. 279-280
Close-up of an 18th-century Persian-forged Damascus steel sword
Carbon nanotubes are long chains of carbon held together by the strongest bond in all chemistry, the sacred sp2 bond, even stronger than the sp3 bonds that hold together diamond. Carbon nanotubes have numerous remarkable physical properties, including ballistic electron transport (making them ideal for electronics) and so much tensile strength that they are the only substance that could be used to build a space elevator. The specific strength of carbon nanotubes is 48,000 kN·m/kg, the best of known materials, compared to high-carbon steel’s 154 kN·/kg. That’s 300 times stronger than steel. You could build towers hundreds of kilometers high with it.
From Arab Seafaring by George F. Hourani:
http://www.muslimheritage.com/article/filling-gap-history-pre-modern-industry-1000-years-missing-islamic-industry
The origins of Iron-working in India
New evidence from the Central Ganga Plain and the Eastern Vindhyas
By Rakesh Tewari
[Director, U.P. State Archaeological Department, Roshan-ud-daula Kothi,
Kaisarbagh, Lucknow 226 001 (U.P.) India (Email: rakeshlko@rediffmail.com)]
Kaisarbagh, Lucknow 226 001 (U.P.) India (Email: rakeshlko@rediffmail.com)]
Recent excavations in Uttar Pradesh have turned up iron artefacts, furnaces, tuyeres and slag in layers radiocarbon dated between c. BCE 1800 and 1000. This raises again the question of whether iron working was brought in to India during supposed immigrations of the second millennium BCE, or developed independently.
Introduction
The date and origin of the introduction of iron artefacts and iron working into India has remained a much debated research problem, not unconnected with the equally debatable question of its association with the supposed arrival, in the second millennium BCE, of immigrants from the west, as often suggested on the basis of the Rigveda. Around the middle of the last century, iron-working origins in India were dated to c. 700-600 BCE (Gordon 1950; Wheeler 1959). Subsequently, a combination of an association with Painted Grey Ware (PGW) and the advent of radiocarbon dating began to push this date back towards the second millennium BCE, a period which had in fact favoured by some scholars earlier in the early twentieth century (Chakrabarti 1992: 10-12).
Considering the radiocarbon dates for the iron bearing deposits at Ataranjikhera in Uttar Pradesh (Table 1) and Hallur in Karnataka, and stratigraphic position of iron in the lower levels mainly at Kausambi near Allahabad, Jakhera in district Etah in the Ganga Valley, and Nagda and Eran in central India, dates around 1000 BCE were suggested (Subramanyam 1964; Banarjee 1965; Chakrabarti 1974; Nagarajarao 1974). At the same time Chakrabarti (1974: 354) challenged the view of a western origin, stating “there is no logical basis to connect the beginning of iron in India with any diffusion from the west, from Iran and beyond”, and further (1976: 122) “that India was a separate and possibly independent centre of manufacture of early iron.”
Since then there has been fresh evidence for even earlier iron-working in India. Technical studies on materials dated c. 1000 BCE at Komaranhalli (Karnataka) showed that the smiths of this site could deal with large artefacts, implying that they had already been experimenting for centuries (Agrawal et al. 1985: 228-29). Sahi (1979: 366) drew attention to the presence of iron in Chalcolithic deposits at Ahar, and suggested that “the date of the beginning of iron smelting in India may well be placed as early as the sixteenth century BCE” and “by about the early decade of thirteenth century BCE iron smelting was definitely known in India on a bigger scale”. On the basis of four radiocarbon measurements, ranging between 3790 + 110 BP and 3570 + 100 BP, available for the Megalithic period (without iron) Sharma (1992: 64, 67) has proposed a range of 1550-1300 BCE (uncalibrated) for the subsequent iron bearing period at Gufkral (Jammu & Kashmir).
On the basis of this evidence a date of around 1300/1200 BCE has been suggested for the beginning of iron in India and c. 800 BCE for the mid Ganga Valley (Allchin & Allchin 1982: 345; Prakash & Tripathi 1986: 568; Gaur 1997: 240). Chakrabarti (1992: 68, 164; 1999: 333) has observed that at Ahar it would be the first quarter of the second millennium BCE and in Malwa soon after the middle of the second millennium BCE. However, the early dates for iron at Ahar are refuted on the grounds of uncertain stratigraphy (Gaur 1997: 244). As far as Komaranhalli is concerned, it is stated that the TL dates have large errors and hence uncertain (Agrawala 2000: 197, 200).
Table 1. Dates* for early iron-use from Indian sites
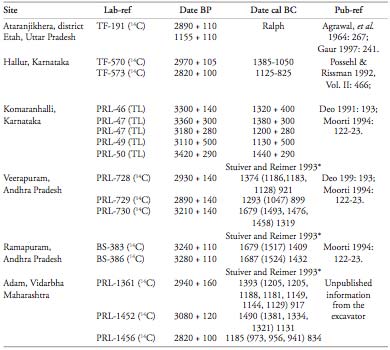
* These dates are calibrated by Dr B. Sekar, BSIP, Lucknow. References for datasets used: Stuiver, et al. 1998a. 537
More recently, early contexts containing iron at Jhusi, located on the confluence of the Ganga and Yamuna in district Allahabad, have been dated to 1107-844 cal BCE (Tewari et al. 2000: 93). Komaranhalli (Karnataka) has given TL dates in the twelfth – fifteenth century BCE, while the radiocarbon dates for early Iron Age sites of Veerapuram and Ramapuram (Andhra Pradesh) are sixteenth – eleventh century cal BCE (Table 1) (Deo 1991: 193; Moorti 1994: 122-23) while in Vidarbha region (Maharastra), contexts containing iron have given radiocarbon dates between the fourteenth and tenth centuries cal BCE (Table 1).
Recent Findings in Uttar Pradesh
This paper briefly reports the results of some recent excavations conducted by the Uttar Pradesh State Archaeological Department under the leadership of the present author and their implications for understanding the beginning of iron-working in the Central Ganga Plain and the adjacent part of the Vindhyas.
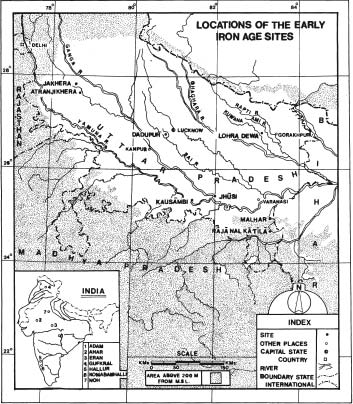
Map showing locations of the Early Iron Age sites in the Central Ganga Plain, the Eastern Vindhyas, and different regions of India.
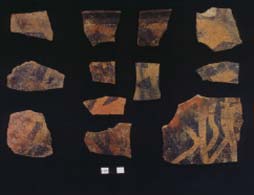
This has further implications in defining the beginning of iron in the subcontinent as a whole. The excavated sites are Raja Nala-ka-tila (199698), Malhar (1998-99), Dadupur (1999-2001) and Lahuradewa or Lohradewa (2001-2002) (Figure 1) Raja Nala-ka-tila (Lat. 24°41’ 55” N.; Log. 83°19’ E.) is located in the upper reaches of the Karamnasa within its loop like meander in district Sonbhadra. The excavations revealed a sequence which has been divided into four periods (Tewari & Research Srivastava 1997; 1998).
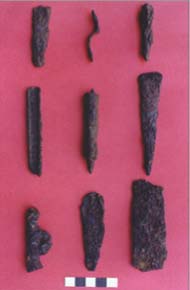
In Period I, no metal was fund and is stratigraphically continuous into Period II. Period III is characterised by the presence of Northern Black Polished Ware (NBPW). Period IV is defined as a Gupta/ post Gupta phase. Iron was found in pre-NBPW deposits (1.5 to 2.00m thick) of Period II in association of the pottery hitherto supposed to be the characteristics of the Chalcolithic period, placed between early to late second millennium BCE, in the area concerned.
The main associated ceramic industries were plain and painted black-and-red black slipped and red wares, in forms which included footed bowl, legged bowl with perforated base, pedestal bowl and button-based goblet. Some sherds also showed cord impressions. Evidence for iron-working included slag and iron artefacts such as a nail, arrowhead, knife and a chisel Radiocarbon dates for the iron bearing deposits range between 1400 and 800 cal BCE.
Table 2. New 14C dates for early iron-use from the Ganga Plain and the Eastern Vindhyas
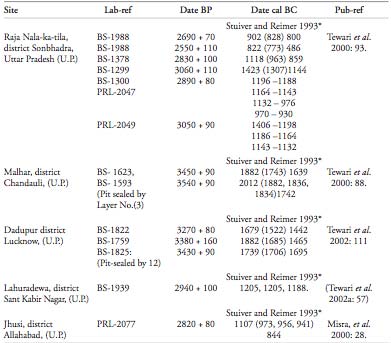
* These dates are calibrated by Dr B. Sekar, BSIP, Lucknow. References for datasets used: Stuiver, et al. 1998a.
Since the date for the introduction of iron in the middle and lower Ganga Valley was being considered as c. 800 BCE (above), its appearance in c. 1400/1300 cal BCE at Raja Nala-ka-tila posed new questions. Realising that this should not be the only site with such early evidence and that there should be examples of experimental iron-smelting which were earlier still, we started a new search. These efforts were rewarded in locating a potential site near a village called Malhar.
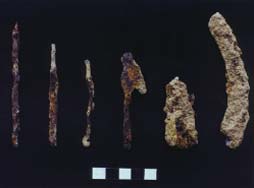
Malhar (district Chandauli; Lat. 24°59’ 16” N.; Long. 83°15’ 46” E.) is on the bank of the Karamnasa which at this point flows through a rocky, haematite-rich terrain before joining the Ganga near Banaras. The excavations carried out at this site also revealed a sequence of four periods: defined as Period I: Pre Iron; Period II: Early Iron; Period III: NBPW; Period IV: BCE 200 to 300 AD (Tewari et al. 2000: 69-98). There is no stratigraphic interval between the layers of Period I and Period II. Iron is present in all the layers of Period II,and identified finds include a nail, clamp, spear-head, arrow-head, awl, knife, bangle, sickle and plough share. As well as iron slag, there were tuyeres and several elongated clay structures, with a burnt internal surface. The ceramic industries of this period are represented by mainly red, black-and-red, black slipped, and grey wares. Red ware and black-and-red ware sherds bearing cord impressions on their exterior were found in greater number in the lower levels. The presence of the coarse variety of corded potsherds implies that the iron appeared earlier here than in Period II at Raja Nala-ka-tila. This assumption was endorsed by two radiocarbon dates ranging around 1800 cal. BCE (Table 2).

Important cultural components of the early iron Naugarh kot suggest that large-scale iron bearing deposits, showing corded ware sherds, iron artefact, slag, smelting activities continued at these sites tuyere, stone and bone artefacts, painted and incised potsherds, for a long time. stone and terracotta beads. Period II, Malhar, Dist. Chandauli.
The area around Malhar may have been something of a centre of iron production. A small mound, of a kind known locally as lohsan or lohsanwa, about 500m south to the main site of Malhar, which looks like a heap of iron slag, on excavation revealed two damaged clay furnaces, one of them is illustrated here as Figure 6, filled with iron slag along with a few sherds of the red, grey, and black slipped wares, an axe, and tuyeres. Survey revealed several lohsanwa sites near Musakhand village, the site known as Phakkada Baba located within the Musakhand dam, to the north-west of Malhar, on Baba Wali Pahari (Tewari et al. 2000) and near Naugarh kot (Singh et al. 2000: 143). Plans of damaged clay furnaces within heaps of iron slag along with tuyeres stuck with smelted iron, and potsherds of the grey, black slipped, NBP and red wares were found at these sites. The pottery assemblage at Phakkada Baba also included examples of dish or bowl-on-stand and other forms, comparable to those from Malhar Period II, in red ware, and black-and-red ware. This extraordinary concentration of iron-slag heaps on Baba Wali Pahari and Naugarh kot suggests that large-scale iron smelting continued at these sites for a long time.
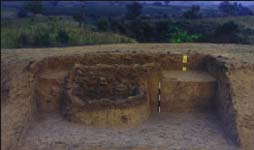
As discussed elsewhere (Tewari et al. 2000) the sites at Malhar, the Baba Wali Pahari, and the Valley are archaeologically linked to the area of Geruwatwa Pahar which appears to have been a major source of iron ore. The Geruwatwa Pahar situated to the southeast of the Baba Wali Pahari, is full of hematite. Villagers reported (as a tradition passed down from several generations), that the agarias (a particular tribe known for their iron smelting skills) from Robertsganj side, used to come in this area to procure iron by smelting the hematite. Probably hematite was being primarily smelted at the Baba Wali Pahari and carried over to the valley sites (situated at a distance of about 6-8 km) for secondary smelting. The presence of tuyeres, slags, finished iron artefacts, above-mentioned clay structures with burnt internal surfaces and arms, revealed at Malhar, suggest a large scale activity related to manufacture of iron tools. It appears that smelted iron was being carried to this site to manufacture the artefacts and the clay structures were used as the furnaces for forging purposes. Thus this part of the Karamnasa Valley would have been a regional centre for iron production and the Malhar a workshop-site for the manufacturing of the iron artefacts.
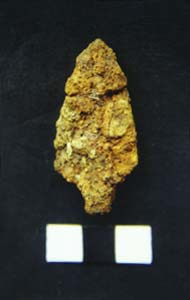
Dadupur (26°42’ N: 80°49’ E) is in the valley of the Sai, a minor Gangatributary near Lucknow. It is the earliest dated site (Tewari et al. 2002:111) between the Gomati and the Sai rivers. The excavations at this site have revealed a sequence divided into three periods. The cultural material of Period-I consists of iron artefacts such as the arrowheadm shown in Figure 7. Red ware dominates the pottery assemblage of this period, while the black-and-red ware is nominally represented. Three radiocarbon dates lie between the eighteenth and sixteenth centuries BCE (Table 2). Period II and III are characterised respectively by the presence of Painted Grey Ware (PGW) and NBP ware.
Lahuradewa (district Sant Kabir Nagar; 26°46’ N; 82°-57’E) is in the trans-Sarayu plain, the Sarayu being a major tributary of the Ganga. The excavations have revealed new information regarding the early farming cultures of the Sarayupar region, including evidence for the domestication of rice (Oryza sativa) in Period I, radiocarbon dated to c. sixth and fifth millennium BCE. Associated ceramics include mostly plain and corded, hand made red, and black-and-red, besides, some grey, and black ware sherds. Period II is marked by the appearance of copper. Pottery of the preceding period continued and a new type of pottery, i.e. black slipped ware is added, and the forms include pedestal bowl, and dish or bowl-on-stand. Iron artefacts appear in Period III in the form of corroded nails and other objects. Other components of the assemblage, however, are the same as in Period II. A radiocarbon date obtained for this level was thirteenth – twelfth century BCE (Tewari et al. 2002a: 57) (Table 2).
As per K.S. Saraswat’s observations (pers.comm.), the carbonised material dated from the sites mentioned above included the branches of some trees, such as Acacia sp., Madhuca indica, Dalbergia sissoo, Treura nudiflora, Boswellia serrata, Aegle marmelos, Syzygium sp., Tectona grandis, Butea monosperma, Logerstroemia sp., Bambusaa sp., etc., and the shrubs like Zixiphus sp., Capparis saparia, Carissa opaca. The above species are in mixed content, with the carbonised remains of leaves, stems and seeds of a number of seasonal herbs and grasses. These tropical vegetations referred to above have generally 60-70 yrs of average life span in case of trees and the shrubs and herbs survive hardly from two to three months to the maximum period of a year or two.
There are other observations on the assemblages from these four sites which might be significant. Copper has been found in a lesser proportion in comparison to iron; presence of burnt clay chunks bearing reed and straw marks and postholes are indicative of wattle and daub houses and thatched huts; associated finds include mainly bone arrowheads, terracotta, stone and steatite (?) beads; some storage bins are dug into the surface and bases of the large earthen storage vessels are represented at Lahuradeawa and Raja Nala-ka-tila; a large quantity of faunal and carbonised archaeo-botanical remains have been recovered at all the sites. As a whole the assemblage is suggestive of well equipped and permanent settlements.
Discussion
These results indicate that iron using and iron working was prevalent in the Central Ganga Plain and the Eastern Vindhyas from the early second millennium BCE. The dates obtained so far group into three: three dates between c. 1200-900 cal BCE, three between c. 1400-1200 cal BCE, and five between c. 1800-1500 cal BCE. The types and shapes of the associated pottery are comparable to those to be generally considered as the characteristics of the Chalcolithic Period and placed in early to late second millennium BCE. Taking all this evidence together it may be concluded that knowledge of iron smelting and manufacturing of iron artefacts was well known in the Eastern Vindhyas and iron had been in use in the Central Ganga Plain, at least from the early second millennium BCE. The quantity and types of iron artefacts, and the level of technical advancement indicate that the introduction of iron working took place even earlier. The beginning of the use of iron has been traditionally associated with the eastward migration of the later Vedic people, who are also considered as an agency which revolutionised material culture particularly in eastern Uttar Pradesh and Bihar (Sharma 1983: 117-131). The new finds and their dates suggest that a fresh review is needed. Further, the evidence corroborates the early use of iron in other areas of the country, and attests that India was indeed an independent centre for the development of the working of iron.
Acknowledgements
I am thankful to Dr Rajagopalan and Dr B.Sekar, Birbal Sahni Institute for Palaeobotany, Lucknow for the determination of 14C dates, to Dr Sekar for the calibration of most of the 14C dates, to Dr KS. Saraswat – a renowned archaeobotanist of the same institution – for the observations regarding the material radiocarbon dated, to Dr P.C. Pant and the Editor, Antiquity for the input to improve the manuscript and to Shri Ram Gopal Mishra and Shri Manmohan Dimri for the figures which illustrate this paper.
References
AGARWAL, D.P. 2000. Ancient Metal Technology and Archaeology of South Asia. New Delhi: Aryan Books International.
AGRAWAL, D.P., S. KUSUMGAR & R.P. SARNA 1964. Radiocarbon dates of Archaeological samples, Current Science 33: 266-69.
AGRAWAL, O.P., H. NARAIN AND G.P. JOSHI 1985. Iron Objects from South Indian Megaliths (Karnataka)
– A Technological Study and Significance, in Sundara, A. (ed.), Archaeology in Karnataka: 219– 234. Mysore: Directorate of Archaeology & Museums.
ALLCHIN, BRIDGET & RAYMOND 1982. The Rise of Civilization in India and Pakistan. Cambridge.
BANARJEE, N. R. 1965. The Iron Age in India. Delhi.
CHAKRABARTI, D.K. 1974. Beginning of Iron in India: Problem Reconsidered, in A.K. Ghosh (ed.), Perspectives in Palaeoanthropology: 345-356. Calcutta: Firma K.L. Mukhopadhyay.
–1976. The beginning of iron in India. Antiquity 4: 114-124.
–1992. The Early Use of Iron in India. Delhi: Oxford University Press.
–1999. India An Archaeological History. Delhi: Oxford University Press.
DEO, S.B. 1991. New Discoveries of Iron Age in India, in C. Margbandhu, K.S. Ramachandran, A.P. Sagar & D.K. Sinha (eds.), Indian Archaeological Heritage I: 189-97. New Delhi: Agam Kala Prakashan.
GAUR, R.C. 1997. Studies in Indian Archaeology and Ancient India I. Jaipur: Publication Scheme, pp. 238-250.
GORDON, D.H. 1950. The Early Use of Metals in India and Pakistan, Journal of the Royal Anthropological Institute, 55-78.
MOORTI, U.S. 1994. Megalithic Culture of South India: Socio-Economic Perspectives, Varanasi, Ganga Kaveri Publishing House.
NAGARAJARAO, M.S. 1974. Iron Age in South India: Fresh Evidence on Chronology, in A.K. Ghosh (ed.), Perspective in Palaeoanthropology: 357-62. Calcutta: Firma K.L. Mukhopadhyay.
POSSEHL, G.L. & P.C. RISSMAN 1992. The Chronology of Prehistoric India: From Earliest Times to the Iron Age, in R.W. Ehrich (ed.) Chronologies in Old World Archaeology, Vol. I: 465-490; Vol. II: 447-474.Chicago and London: The University of Chicago Press.
PRAKASH, B. & V. TRIPATHI 1986. Iron technology in ancient India, Historical Metallurgy: 568-579.
SAHI, M.D.N. 1979. Iron at Ahar, in D.P. Agrawal &
D.K. Chakrabarti (eds.). Essays in Indian
Protohistory. Delhi: pp. 365-68.
SHARMA, A.K. 1992. Early Iron Users of Gufkral, in Nayak B.U. & N.C. Ghosh (eds.), New Trends in Indian Art and Archaeology I: 63-68. New Delhi: Aditya Prakashan.
SHARMA, R.S. 1983. Material Culture and Social Formations in Ancient India. Delhi: Macmillan.
SINGH, P., R. TEWARI & R. N. SINGH 2000. Explorations in Chandauli District (U.P.) 19992000: A Preliminary Report, Pragdhara 10: 135148.
SUBRAMANYAM, B.R. 1964. Appearance and Spread of Iron in India – An Appraisal of Archaeological Data, Journal of the Oriental institute, Baroda 13: 349-59.
TEWARI, R., & R. K. SRIVASTAVA 1997. Excavations at Raja Nala-ka-tila (1995-96), District Sonbhadra (U.P.): Preliminary observations, Pragdhara 7: 77
95.
–1998. Excavations at Raja Nala-ka-tila (1996-97) District Sonbhadra (U.P.): Preliminary Observations, Pragdhara 8: 99-105.
TEWARI, R., R.K. SRIVASTAVA, K.S. SARASWAT & K.K. SINGH 2000. Excavations at Malhar, District Chandauli (U.P.) 1999: A Preliminary Report, Pragdhara 10: 69-98.
TEWARI, R., R.K. SRIVASTAVA, & K.K. SINGH 2002. Dadupur Excavations 1999-2000-2001, District Lucknow, Uttar Pradesh: A Preliminary Report, Pragdhara 12: 99-116.
TEWARI, R., R.K. SRIVASTAVA, & K.K. SINGH 2002a. Excavation at Lahuradewa, District Sant Kabir Nagar, Uttar Pradesh, Puratattva 32: 54-62.
WHEELER, R.E.M. 1959. Early India and Pakistan. London.
AGRAWAL, D.P., S. KUSUMGAR & R.P. SARNA 1964. Radiocarbon dates of Archaeological samples, Current Science 33: 266-69.
AGRAWAL, O.P., H. NARAIN AND G.P. JOSHI 1985. Iron Objects from South Indian Megaliths (Karnataka)
– A Technological Study and Significance, in Sundara, A. (ed.), Archaeology in Karnataka: 219– 234. Mysore: Directorate of Archaeology & Museums.
ALLCHIN, BRIDGET & RAYMOND 1982. The Rise of Civilization in India and Pakistan. Cambridge.
BANARJEE, N. R. 1965. The Iron Age in India. Delhi.
CHAKRABARTI, D.K. 1974. Beginning of Iron in India: Problem Reconsidered, in A.K. Ghosh (ed.), Perspectives in Palaeoanthropology: 345-356. Calcutta: Firma K.L. Mukhopadhyay.
–1976. The beginning of iron in India. Antiquity 4: 114-124.
–1992. The Early Use of Iron in India. Delhi: Oxford University Press.
–1999. India An Archaeological History. Delhi: Oxford University Press.
DEO, S.B. 1991. New Discoveries of Iron Age in India, in C. Margbandhu, K.S. Ramachandran, A.P. Sagar & D.K. Sinha (eds.), Indian Archaeological Heritage I: 189-97. New Delhi: Agam Kala Prakashan.
GAUR, R.C. 1997. Studies in Indian Archaeology and Ancient India I. Jaipur: Publication Scheme, pp. 238-250.
GORDON, D.H. 1950. The Early Use of Metals in India and Pakistan, Journal of the Royal Anthropological Institute, 55-78.
MOORTI, U.S. 1994. Megalithic Culture of South India: Socio-Economic Perspectives, Varanasi, Ganga Kaveri Publishing House.
NAGARAJARAO, M.S. 1974. Iron Age in South India: Fresh Evidence on Chronology, in A.K. Ghosh (ed.), Perspective in Palaeoanthropology: 357-62. Calcutta: Firma K.L. Mukhopadhyay.
POSSEHL, G.L. & P.C. RISSMAN 1992. The Chronology of Prehistoric India: From Earliest Times to the Iron Age, in R.W. Ehrich (ed.) Chronologies in Old World Archaeology, Vol. I: 465-490; Vol. II: 447-474.Chicago and London: The University of Chicago Press.
PRAKASH, B. & V. TRIPATHI 1986. Iron technology in ancient India, Historical Metallurgy: 568-579.
SAHI, M.D.N. 1979. Iron at Ahar, in D.P. Agrawal &
D.K. Chakrabarti (eds.). Essays in Indian
Protohistory. Delhi: pp. 365-68.
SHARMA, A.K. 1992. Early Iron Users of Gufkral, in Nayak B.U. & N.C. Ghosh (eds.), New Trends in Indian Art and Archaeology I: 63-68. New Delhi: Aditya Prakashan.
SHARMA, R.S. 1983. Material Culture and Social Formations in Ancient India. Delhi: Macmillan.
SINGH, P., R. TEWARI & R. N. SINGH 2000. Explorations in Chandauli District (U.P.) 19992000: A Preliminary Report, Pragdhara 10: 135148.
SUBRAMANYAM, B.R. 1964. Appearance and Spread of Iron in India – An Appraisal of Archaeological Data, Journal of the Oriental institute, Baroda 13: 349-59.
TEWARI, R., & R. K. SRIVASTAVA 1997. Excavations at Raja Nala-ka-tila (1995-96), District Sonbhadra (U.P.): Preliminary observations, Pragdhara 7: 77
95.
–1998. Excavations at Raja Nala-ka-tila (1996-97) District Sonbhadra (U.P.): Preliminary Observations, Pragdhara 8: 99-105.
TEWARI, R., R.K. SRIVASTAVA, K.S. SARASWAT & K.K. SINGH 2000. Excavations at Malhar, District Chandauli (U.P.) 1999: A Preliminary Report, Pragdhara 10: 69-98.
TEWARI, R., R.K. SRIVASTAVA, & K.K. SINGH 2002. Dadupur Excavations 1999-2000-2001, District Lucknow, Uttar Pradesh: A Preliminary Report, Pragdhara 12: 99-116.
TEWARI, R., R.K. SRIVASTAVA, & K.K. SINGH 2002a. Excavation at Lahuradewa, District Sant Kabir Nagar, Uttar Pradesh, Puratattva 32: 54-62.
WHEELER, R.E.M. 1959. Early India and Pakistan. London.