- Worlds Largest Bronze Nataraja.This is the largest bronze Nataraja in the world approx. 8ft high, bigger than the Chidambaram Nataraja.Chola Bronze at Thirunallam. Konerirajapuram is about half hour drive from Kumbakonam, in Mayiladithurai taluka of Nagapattinam district in Tamil Nadu.
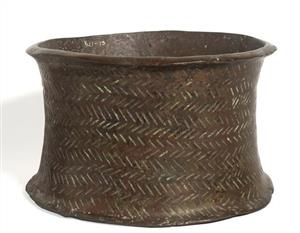
The word dhokra is represented as a hieroglyph on two Indus seals from Dholavira and Mohenjo-daro. Now we know that the word means 'cire perdue' or lost-wax technology for metal alloys to create bronze/brass statues, tools and weapons. This was arrival of the bronze age with a bang! contributed by dhokra artisans who live today in India and are called dhokra kamar.
Hieroglyph:
ḍŏkuru-ḍŏkuru; । कुब्जावस्था m. (sg. dat. ḍŏkaris-ḍŏkaris ड्वकरिस््-ड्वकरिस् ), the condition of a bent or humpbacked person (from old age, injury to the spine, or the like). Cf. ḍŏkhürü and dọ̆ku. -- dyunu -- । कार्श्ये&1;पि कार्यविधानम् m.inf. to do a little work as best one can when one is bent by old age.(Kashmiri) 1. Ku. ḍokro, ḍokhro ʻ old man ʼ; B. ḍokrā ʻ old, decrepit ʼ(CDIAL 5567).
ټوقړ ṯṯūḳaṟṟ s.m. (5th) An old or decrepit man. Pl.ټوقړان ṯṯūḳaṟṟān. See ټاقړ (Pashto)
?Allograph: 1. N. ḍhoknu, ḍhognu ʻ to bow down before, salute respectfully ʼ; H. ḍhoknā ʻ to lean against ʼ; -- Ku. ḍhok ʻ obeisance ʼ, N. ḍhok, ḍhog -- bheṭ (whence -- g in verb), H. ḍhok f., OMarw. ḍhoka f.2. H. dhoknā ʻ to bow down before ʼ, dhok f. ʻ obeisance ʼ.(CDIAL 5611). Go. (Mu.) doṛī- to bow (DEDR 3525).
தொக்கடி tokkaṭi , n. (W .) 1. A kind of ola covering to protect fruits on the tree; மரத் திற் பழங்களைப் பொதிந்துவைக்கும் ஓலைமறைவு. 2. A small ola-basket for fruit; பழம் வைக்குஞ் சிறு கூடை. See other etyma embedded from CDIAL in an earlier blogpost URL cited.
Rebus:
Hieroglyph:
ḍŏkuru-ḍŏkuru
ټوقړ ṯṯūḳaṟṟ s.m. (5th) An old or decrepit man. Pl.
Rebus:
dŏkuru परिघः a kind of hammer for use in metal-work, with a drum-shaped head. (El. dauker; L. 46, dokar; Śiv. 1563.) dŏkȧri-dab दब् । कूटाघातः m. hitting with a hammer, esp. the welding together of heated metal. -- dan -दन् । लघुकूटदण्डः m. the wooden handle of such a hammer. (Kashmiri)
धोकाळ [ dhōkāḷa ] m C A large blazing fire.(Marathi)
धोकाळ [ dhōkāḷa ] m C A large blazing fire.(Marathi)
dukra
Dhokra kamr or gharua of Bankura, Purulia, Midnapore, Burdwan in West Bengal, Malhars of Jharkhand and Sithrias of Orissa and Vis'wakarma of Tamil Nadu and Kerala also use the dhokra technique of metal casting.
That we are discussing dhokra art still practiced in India today may be seen
from
http://bharatkalyan97.blogspot.in/2014/01/meluhha-metallurgical-roots-and-spread.html
![]()
Dhokra. Mother with five children.

"The specialty of Dhokra handicraft is that each relic seems to have been made up of a seamless wire coiled around the clay article. This is indeed an illusion as the metal casting is done using the lost-wax technique which forms the main attraction of this craft. It is believed that the lost-wax technique for copper casting had been found in other East Asian, Middle-East and Central American regions as well. In Purulia, the Dhokras make mixed aluminum by the lost wax process but do not make any images or figures; they rather make paikona, dhunuchi, pancha pradeep, anklets, and ghunghrus.
Dhokra metal casting is generally famous for unique artefacts like animals, jewelry, piggybank (Buli), ornamented pots and various deities. In the genre of jewelry: payeri (anklets), hansuli (necklace), earrings and bangles are most in demand because of the style statement they impart. The single and multiple diya lamps are, even molded in the forms of elephants, and are considered auspicious for many Hindu occasions. Dhokra is the only live example of the metal casting in the East India as other similar crafts have faded away with time. But unfortunately, no substantial initiatives have been taken to promote and help sustain the Dhokra art in recent times in West Bengal." http://indianscriptures.com/vedic-society/arts/arts-and-traditions-of-west-bengal
"Carbon-14 dating of the reed mat in which the objects were wrapped suggests that it dates to at least 3500 B.C." http://www.metmuseumorg/toah/hd/nahl/hd_nahl.htm
" I-1819, which comes from a piece of cloth found in a burial in nearby Cave 2, is slightly younger, but another short-lived sample, I-616 from the Cave of Horror at Nahal Hever, gave a result in the late 5th millennium." https://journals. uair.arizona.edu/index.php/ radiocarbon/article/viewFile/ 879/884
תודה על המאמר. מעיון ראשון, ההתיחסות למטמון נחל משמר מענינת אבל דורשת עדכון- סדרת תאריכי פחמן חדשה יחסית (2011) מצביעה על 4400± לפנה״ס, לא סוף האלף ה ד׳.
להתראות, עוזי.
A surprise that these were found in a shipwreck in Haifa !
Dhokra cire perdue (lost-wax) is a brilliant bronze age invention and should herald a new approach to explain the hieroglyphs on thousands of cylinder seals of the Fertile Crescent right from the chalcolithic times (ca. 5th millennium BCE -- now based on Nahal Mishmar new carbon-14 datings) into the bronze age.
………………..Dr. Uzi Avner
I deeply appreciate the help provided by Dr. Uzi Avner for this update. I will provide the 2011 citation for the new C-14 dating in an addendum in due course.
Dr. Uzi Avner notes that "The first seminar, the reference in Nahal Mishmar hoard interesting but requires updating - a series of dates Carbon relatively new (2011) indicates ± 4400 BC, not the end of the fourth millennium."
Dr. Uzi Avner notes that "The first seminar, the reference in Nahal Mishmar hoard interesting but requires updating - a series of dates Carbon relatively new (2011) indicates ± 4400 BC, not the end of the fourth millennium."
This insight of Dr. Uzi Avner has a profound impact on chronology studies of the evolution of bronze age and writing systems.
Presence of dhokra (lost-wax artisans) in Nahal (Nachal) Mishmar is stunning and points to ancient Israel-India connections from 5th millennium BCE. I had noted that the two pure tin ingots found in Haifa shipwreck had Meluhha hieroglyphs to denote tin. ranku 'antelope'; ranku 'liquid measure' Rebus: ranku 'tin (cassiterite) ore'. S. Kalyanaraman, 2010, The Bronze Age Writing System of Sarasvati Hieroglyphics as Evidenced by Two “Rosetta Stones” - Decoding Indus script as repertoire of the mints/smithy/mine-workers of Meluhha, Journal of Indo-Judaic Studies, Number 11, pp. 47-74
Dhokra cire perdue (lost-wax) is a brilliant bronze age invention and should herald a new approach to explain the hieroglyphs on thousands of cylinder seals of the Fertile Crescent right from the chalcolithic times (ca. 5th millennium BCE -- now based on Nahal Mishmar new carbon-14 datings) into the bronze age.
Also that harosheth hagoyim is cognate with kharoṣṭī goya lit. 'blacksmith lip guild'.
It is interesting that Dr. Moti Shemtov refers to Nahal Mishmar as Nachal Mishmar. It is similar to the change from Meluhha to Mleccha !
This Nahal Mishmar copper stand might have held a storage pot with a pointed bottom or a pot like the Susa pot which had a 'fish' hieroglyph and metal artifacts of tools and vessels. The Meluhha hieroglyph 'fish' read: ayo'fish' (Munda) Rebus: ayo'metal alloy' (Gujarati. Pali)
It could also have held a Burzahom type-pot with beads and a buffalo-horn hieroglyph.
Glyph: kuṇḍī ‘crooked buffalo horns’ (Lahnda.) Rebus: kuṇḍī = chief of village (Prakrit). The artisan is kundakara—m. ‘turner’ (Skt.); H.kũderā m. ‘one who works alathe, one who scrapes’ (CDIAL 3297). ḍabe, ḍabea‘large horns, with a sweeping upward curve, applied to buffaloes’ (Santali) Rebus: ḍab, ḍhimba, ḍhompo ‘lump (ingot?)’, clot, make a lump or clot, coagulate, fuse, melt together (Santali) கண்டி kaṇṭi buffalo bull (Tamil) Pk. gaḍa -- n. ʻlarge stoneʼ? (CDIAL 3969) K. garun, vill. gaḍun ʻ to hammer into shape, forge, put together ʼ. (CDIAL 3966). kaḍiyo [Hem. Des. kaḍa-i-o = (Skt. Sthapati, a mason) a bricklayer, mason (G.)]English: Pot depicting horned figure. Burzahom (Kashmir), 2700 BC. National Museum, New Delhi. Noticed in the museum : the pot depicts horned motifs, which suggests extra territorial links with sites like Kot-Diji, in Sindh.
Français : Pot orné d'incisions et de motifs peints portant de grandes cornes recourbées, qui laissent supposer des liens extra territoriaux avec des sites tels que Kot-Diji, dans le Sindh. H env. 50cm. Site archéologique de Burzahom (Kashmir) daté 2700 av. J.-C. Musée National, New Delhi
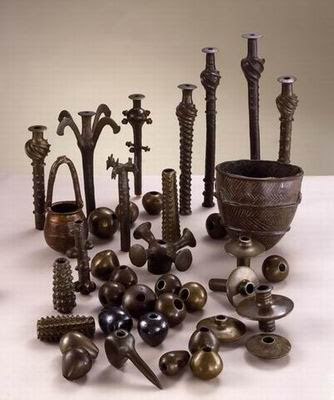
The most common objects were 118 of these "standards" or "scepters." What they really were is anybody's guess. Some had traces of reeds or wood in the holes, suggesting that they were attached to poles.
There are ten of these cylindrical objects in the hoard. They are conventionally known as "crowns," but more archaeologists think they were stands for vessels with pointed bottoms.
What is one to make of this hippopotamus ivory object, essentially a slice from a hippo's tooth drilled with as many holes as would fit?
This object seems to be proof that the pushmi-pullyu really existed in the Chalcolithic era.
The closest major site of this period is a shrine at the oasis of Ein Gedi, 7 miles (12 km) away, and the objects may have been hiddenwhen the shrine was under some kind of threat. The cave is in a steep ravine, accessible only with ropes and ladders, so it would have made a good hiding place. So good that this amazing collection of objects remained hidden for 5500 years.
FRIDAY, APRIL 6, 2012
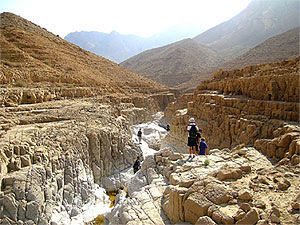
Most treasure objects are made of copper containing a variable percentage of arsenic, but always high ( 4 % -12 %). Most surprising is that this special copper was used only on objects made with the lost wax technique rather simple chisels and hammers, lso found that 16. This distinction is also present in other sites . There is therefore a clear difference in the use of the two types of copper . For votes almost pure copper was used , although softer , for special objects no longer , harder and easier to empty arsenical copper was used.
The whole treasure is a magnificent collection of art objects. The objects are made of valuable materials , maintain high technological quality and have a superior finish . Their shapes witness to a developed artistic sense. It can be assumed , in view of the decorative motifs , which is a rich repository of religious symbolism.
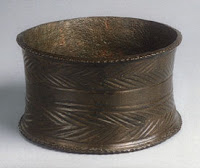
a) Crowns
The cache ten cylindrical objects that seem crowns, with a diameter of 15'6 to 19 inches , and a height of 7 inches to 11'7 found. Two are provided with small feet. The body sometimes takes an incised decoration varied design : parallel lines , triangles and bands as Fishbone .
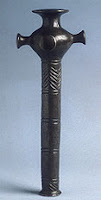
b ) The scepters
This is a group of 118 different objects , with lengths ranging from 7 to 40 inches. Some of the scepters retained traces of wooden handles or cane , and some was a black sticky substance. This has led archaeologists to conclude that the objects were taken on long poles , perhaps in sacred processions. A linen thread found in one of the Sceptres may indicate that they are bound lightweight materials such as tapes . All scepters are similar in shape but differ greatly in their size and detail of its decoration. The most splendid has five heads of animals (four of ibex and an animal with twisty horns) . It should be noted that similar scepters found at other sites .
c ) The poles
This term describes a group of stylized , long and solid scepters . Three of them appear refined versions of scepters with curved ends. The fourth is like the stem of a plant and the fifth has a flat head hooked .
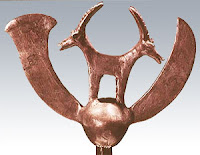
d ) The sets standards
The three splendid banners of this group were definitely mounted on poles . The first is a hollow pear-shaped object with two twins ibex represented with one body , four legs and two heads. Each ibex is facing one of the biggest arms, one ax-shaped and the other knife , leaving the piriform body . The second banner has a short hollow columnilla a rectangular panel that extends from the center , made in the form of a vulture with outstretched wings. The third is more modest ; swelling part of his plans four protruding out in four different directions.
e) The horn-shaped objects
Three objects in the form of curved horn emphasize the importance of the horns in the Chalcolithic ritual. Two of the horns lead schematic figures of birds.
f ) Containers
A jug turtleneck beautiful proportions , a cup or deep bowl and three cups shaped basket with high vertical handle are the only containers found in the treasure.
g) maceheads
The largest group of objects with a total of 261 , including several thickened (rounded , pear-shaped , elongated or discoidal ) forms that are usually called " mace heads " objects. All have a hole in the center to insert a handle . Some specimens preserved remains of wooden handles . The surface is well polished and all undecorated .
Although the mace-head was a common weapon in Mesopotamia and Egypt , these objects may not to be considered as weapons. Their presence in the treasure seems, rather, a ceremonial use. If similarity with convex parts of the banners and scepters supports this view .
Six mace heads were made of hematite , Natural iron oxide . Were emptied but not drilled , as yet no technology known iron work . Another club head is made of hard limestone .
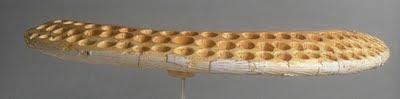
h ) The objects made of hippo tusk
Five mysterious objects were hidden along with objects of copper hippopotamus ivory , sectioned along the tusk shaped scythe. Are perforated by three rows of round holes , and in the middle of each there is a hole with a protruding edge .
i ) Cash ivory
A final object of one type is an ivory box 38 inches long made with a piece of elephant tusk well polished .
Translation from Spanish.http://curiosomundoazul.blogspot.in/2011/07/el-tesoro-de-nahal-mishmar.html
![]() | ||||
Mysteries of the Copper Hoard Fifty years have passed since Pessah Bar-Adon discovered, in a cave in the Judean Desert canyon of Nahal Mishmar, the biggest hoard of ancient artifacts ever found in the Land of Israel: 429 copper objects, wrapped in a reed mat. Five decades and dozens of academic papers after their discovery, the enigma of how and why these 6,000-year-old ritual objects ended up in a remote cave in the Judean Desert is still unsolvedBy Yadin Roman Extracted from ERETZ Magazine, June-July 2011 | ||||
The Forum for the Research of the Chalcolithic Period, "a group of academics interested in this prehistoric age", according to Dr. Ianir Milevski (Israel Antiquities Authority), gathered on June 2 at the Israel Museum in Jerusalem in order to commemorate the fiftieth anniversary of the discovery of the most important find from this period: the Nahal Mishmar copper hoard. After a day of presenting new insights pertaining to the copper objects, the conference wrapped up with a discussion on the source of the items in the cave and the reason they were hidden there. The debate emphasized what has remained unsolved after 50 years of research: while it is widely accepted that the hoard is an assembly of ritual objects, there still is no agreement or plausible reason as to where the objects came from and why they were stashed away. The treasure was found while looking for something completely different. In 1947, Bedouins from the Ta’amireh tribe, who roamed the Judean Desert, discovered ancient parchments hidden in the caves of the sheer cliffs of the canyons leading down to the Dead Sea. Once it was discovered that these brittle parchments could bring in money when sold to dealers in Bethlehem and Jerusalem, the Bedouins turned into avid archaeologists, scouring the desert caves in search of ancient scrolls. In the 1950s, new scrolls sold to the dealers in Bethlehem, which was part of Jordan at the time, led archaeologists working in Jordan to discover letters and other artifacts in Nahal Murabba’at, south of Qumran, where the Dead Sea Scrolls had been found. As more pieces of ancient scrolls began to appear in the antiquities market, it was clear that some of them were coming from the Israeli side of the Judean Desert. The desert border between Israel and Jordan was a straight unmarked line on the map, inaccessible to vehicles. The Bedouins, even if they had heard of the newly set-up border, did not recognize it and crossed over freely from side to side. Immediately after the War of Independence, Prof. Eliezer Sukenik, the dean of Israeli archaeologists and the father of Yigael Yadin, discussed the need to survey the caves on the Israeli side of the Judean Desert. Sukenik had purchased the first three complete Dead Sea Scrolls on the eve of the War of Independence and his son would later purchase the four remaining complete scrolls in New York. The year that Sukenik died, 1953, the first, impromptu Israeli desert cave survey was conducted. |
Addendum on carbon-14 dating of Nahal Mishmar finds to ca. +4400 BCE:
Table 10.6 Radiocarbon determinations from Nahal Mishmar
https://www.academia.edu/attachments/31198898/download_file 10. Developmental Trends in Chalcolithic Copper Metallurgy: A Radiometric Perspective -- Aaron N. Shugar and Christopher J. Gohm
http://www.scribd.com/doc/198085507/Shugar-and-Gohm-Chapter-10-2010-in-Print
Radiometric evidence from Nahal Mishmar (Cave 1) is complicated, as dates both old and new offer contradictory information (Table 10.6). For the most part, these contradictions are related to the dating of the reed mat in which the hoard was wrapped (ARP-series, BM-140, I-285 and W-1341, the last three of which are included here for comparative purposes only, as they were measured very early in the history of the technique and may not be entirely reliable). These nine dates suggest that the mat was an ancient heirloom repaired occasionally over time, as they ‘spread out in at least three groups over a millennium or more … and that such repairs may be responsible for the divergent 14C ages from different portions of the mat’ (Aardsma 2001, 1251–3).
Owing to the incredible variations between these determinations the date of the reed mat contributes little to the present discussion, and instead other samples from Cave 1 should be considered. A sample from another reed mat (RT-1407) yielded a date between the 40th and 37th centuries cal BCE, while a sample from a possible loom fragment (RT-1409) appears to date between the 44th and 41st centuries cal BCE (Carmi and Segal 1992, 131). A third date originating from the haft of one of the copper standards (I-353), between the 40th and 34th centuries cal BCE, also deserves mention despite its age (measured inthe 1960s) (Weinstein 1984, 335). These determinations are not statistically the same, and the sub-periods best represented by these three dates are D followed by E, suggesting significant activity at Nahal Mishmar from the 39th to the 36th centuries cal BC (there is also a concentration of radiocarbon years in sub-period B, but these are strongly outweighed by those of D and E). Based on these determinations and the stratigraphic context of the hoard itself, it would be very difficult to push the date of the hoard’s deposition earlier than the first quarter of the 4th millennium cal BCE (a conclusion also reached by Moorey (1988, 173)).
http://www.scribd.com/doc/56148616/Besenval-Roland-2005 Shahi-Tump leopard weight.
Leopard weight. Shahi-Tump (Balochistan).
Meluhha hieroglyphs; rebus readings: Leopard, kharaḍā; rebus:karaḍā 'hard alloy from iron, silver etc.'; ibex or markhor 'meḍh' rebus: ‘iron stone ore, metal merchant.’
खरडा [ kharaḍā ] A leopard. खरड्या [ kharaḍyā ] m or खरड्यावाघ m A leopard (Marathi). Kol. keḍiak tiger. Nk. khaṛeyak panther. Go. (A.) khaṛyal tiger; (Haig) kariyāl panther Kui kṛāḍi, krānḍi tiger, leopard, hyena. Kuwi (F.) kṛani tiger; (S.) klā'ni tiger, leopard; (Su. P. Isr.) kṛaˀni (pl. -ŋa) tiger. / Cf. Pkt. (DNM) karaḍa- id. (CDIAL 1132+). Rebus 1: kharādī ‘ turner, a person who fashions or shapes objects on a lathe’ (Gujarati) Rebus 2: करड्याची अवटी [ karaḍyācī avaṭī ] f An implement of the goldsmith. Rebus: करडा [karaḍā] Hard from alloy--iron, silver &c. (Marathi)
miṇḍāl ‘markhor’ (Tōrwālī) meḍho a ram, a sheep (G.)(CDIAL 10120); rebus: meḍ (Ho.); mẽṛhet ‘iron’ (Mu.Ho.)mẽṛh t iron; ispat m. = steel; dul m. = cast iron (Munda)
Lothal seal L048 Ibex. Another hieroglyph shown on the seal: ayo 'fish' rebus: ayo 'metal alloy' (Gujarati); ayas 'metal' (Sanskrit)
Fish sign incised on copper anthropomorph, Sheorajpur, upper Ganges valley, ca. 2nd millennium BCE, 4 kg; 47.7 X 39 X 2.1 cm. State Museum, Lucknow (O.37) Typical find of Gangetic Copper Hoards. miṇḍāl markhor (Tor.wali) meḍho a ram, a sheep (G.)(CDIAL 10120) Rebus: meḍh ‘helper of merchant’ (Gujarati) meḍ iron (Ho.) meṛed-bica = iron stone ore, in contrast to bali-bica, iron sand ore (Munda) ayo ‘fish’ Rebus: ayo, ayas ‘metal. Thus, together read rebus: ayo meḍh ‘iron stone ore, metal merchant.’
meḷh ‘goat’ (Br.) Rebus: meḍho ‘one who helps a merchant’ vi.138 ‘vaṇiksahāyah’ (deśi. Hemachandra). Allograph: meṛgo = with horns twisted back; meṛha, m., miṛhi f.= twisted, crumpled, as a horn (Santali)
https://www.academia.edu/4602453/Jarrige_J.-F._Didier_A._and_Quivron_G._2011_Shahr-i_Sokhta_and_the_Chronology_of_the_Indo-Iranian_Borderlands._Paleorient_37_2_7-34
Jarrige_Didier_Quivron_Paleorient37-4.pdf
Shahr-i Sokhta and the chronology of the Indo-Iranian regions -- Jarrige, JF, A. Didier and G. Quivron (2011) Paleorient 37 (2): 7-34.
Svastika designs discussed and presented in this article point to the use of zinc as an alloying metal.
svastika 'glyph' Rebus: sattva, jasta, satthiya 'zinc'.
http://www.scribd.com/doc/198123919/Jarrige-Didier-Quivron-Paleorient37-4-2011
Two methods of lost wax casting are done in Krofofrom. Both techniques begin with a bees wax model, but the method of filling the mold with metal differs. A wax model is made, it is covered with special mixtures to create a mold, the wax is melted out of the mold, then the cavity is filled with molten metal. The first method is demonstrated in Sokoban Krofrom (Krofofrom) by craftsmen at Providence Creation, P.O. Box 11592, Kumasi, Ghana. Telephone: 0244-524998 and 0243-818557. Email:ponsahgh@Ghanayahoo.com. | ||||
![]() | ![]() | ![]() | ![]() | ![]() |
To make the model, bees wax is softened in fire. | Then the wax is pressed over a mold, and cut. | More wax is added to create the details. | They are melted with a hot iron to bond them. | Features are sculpted with a wood tool. |
![]() | ![]() | ![]() | ![]() | ![]() |
A wax thread is rolled out on a table, spiraled, cut in half, then pressed onto the face to form the ears. |
A new quicker method a forming wax models utilizes cement molds to help produce flat, textured pieces. | |||
![]() | ![]() | ![]() | ![]() |
The molds are soaked in water to that the bees wax won't stick. | Warm wax is pressed into the wet mold. | The excess wax is immediately cut away. |
![]() | ![]() | ![]() | ![]() |
The wax is carefully removed. | This other part of the buckle is fabricated. | Voila! The finished wax buckle. |
The next step of the process is to make a mold. | |||
![]() | ![]() | ![]() | ![]() |
Charcoal is pulverized, sifted, then mixed with water and clay to form a fine slurry that will preserve fine details. The wax models are dipped into it, bundled together so that several may be cast at once, then covered with more slurry. The wax rods (gates) will serve as channels for the molten metal. |
![]() | ![]() | ![]() | ![]() |
A thicker slurry covers everything except the top of the wax. | Palm fiber is separated, mixed with clay, then sand is added to the mixture to form the outside of the mold. |
![]() | ![]() | ![]() | ![]() |
The fiber and clay mixture covers the black mold and is used to make a bowl-shaped top and a crucible. | Scrap metal from earlier castings is cut apart, weighed, and then put into the crucible. |
![]() | ![]() | ![]() | ![]() |
The crucible is then attached to the mold with more clay and allowed to dry for a few days. | The dry molds are placed (with the metal side down) into a kiln and covered with a thick layer of charcoal. An electric blower is moved from hole to hole to gradually elevate the temperature. The wax will burn out and the metal will heat to a liquid. | After a few hours, the molds are removed, then turned over so that the metal will flow into the cavity. |
![]() | ![]() | ![]() | ![]() |
Water is occasionally poured over the fire to cool the coals so that the molds that are deep in the kiln may be more easily removed with tongs. The empty kiln awaits the next firing. | A banana stem dipped in wet clay cools and hardens the metal to stop it from leaking out of a crack. | After cooling, the molds are broken open; metal has taken the place of the wax. |
![]() | ![]() | ![]() | ![]() | ![]() |
After cutting off the gates with wire cutters, the burnt black core is removed. | George Owusu removes rough spots on the casting with an electric grinder. | The side and edge of an abrasive cut-off wheel is also used to smooth the metal surface. |
![]() | ![]() |
The pieces are then polished with soft lemons and a wire brush. | The result is amazing! |
The mold making process can be seen in more detail below. Unfortunately, I misplaced the name of the demonstrator, but he works for Mr. John K. Dapaah of Japad Brass Enterprise in Krofofrom, Ghana, Telephone: 0244-613157 and 0244-226605. | |||
![]() | ![]() | ![]() | ![]() |
Wax models are dipped into a slurry of water, clay, and fine charcoal, then dried. The pieces are next dipped into a coarser slurry and bundled together and left to dry. | A wet brush scrubs off the top of the bundle to reveal tiny parts of each embedded clay model. | Wax threads are fused to the top of each model to channel the metal during casting. |
![]() | ![]() | ![]() |
The top of the threads are joined together. | The molds are then dipped into a coarse slurry and left to dry. | The dry mold is then covered with a mixture of clay, sand, and palm fiber. A crucible is made from the same mixture and both pieces are left to dry. |
![]() | ![]() | ![]() |
The dry crucible is filled with clean scrap metal from previous castings. | The opening of the crucible is joined to the top of the mold, then both pieces are covered with the clay fiber mixture, then left to dry completely. |
The other method of casting begins the same way at Mr. Afriyie's Gee Creation (P.O. Box X 397 F. N. T. Ksi., Kumasi, Ghana. Telephone: 0244-791914 and 0242-238487), but metal is heated separately, then poured into the molds. | ||||
![]() | ![]() | ![]() | ![]() | ![]() |
Hollow beads use a core to keep the metal from filling the center of the bead. To make the core mixture, fresh cow dung is collected, the dung is covered with sifted, powdered charcoal and a clay slurry (clay mixed with water). Large pieces are smashed with a wooden pounder before it is mixed by hand to remove all the lumps. | The cores are shaped, then left to dry in the sun. |
![]() | ![]() |
A hollow bead is made by covering the core with wax threads. | The wax is heated over a small clay stove. |
![]() | ![]() | ![]() | ![]() |
The wax threads are made by pushing soft bees wax through an extruder (seen in the background). | The core is covered with extruded wax threads. |
![]() | ![]() | ![]() | ![]() |
As with the first method, the wax models are dipped into a slurry of water, clay and charcoal, bundled together, covered with more slurry, then covered with a coarser clay mixed with palm fiber. | Metal is placed in a crucible, then covered with charcoal. An electric blower helps raise the temperature. |
![]() | ![]() | ![]() | ![]() |
The molds are placed top-down into a kiln, then heated for a few hours with wood until the wax melts out. Scrap plastic is thrown onto the fire right before casting to increase the temperature of the fire. The molds are then removed, turned upright on the ground, and filled with molten metal (brass with a little bit of aluminum). It's ready to cast when blue smoke rises from the molten metal. | The last drop of metal is poured from the crucible (a recycled refrigerator motor housing). |
http://iweb.tntech.edu/cventura/lostwaxcasting.htm
Archaeotechnology See: http://www.tms.org/pubs/journals/JOM/0210/Pillai-0210.html
An Article from the October 2002 JOM
Archaeotechnology See: http://www.tms.org/pubs/journals/JOM/0210/Pillai-0210.html
An Article from the October 2002 JOM
The Lost-Wax Casting of Icons, Utensils, Bells, and Other Items in South India
R.M. Pillai, S.G.K. Pillai, and A.D. Damodaran
Indian artisans and craftsmen have long been masters at extracting and shaping metals and alloys, as proven by archaeological finds from the 2nd–3rd millennia B.C. For example, two well-known artifacts, castings of the dancing girl of Mohenjo Daro and the Mother Goddess of Adichanallur, Tamilnadu, depict a high degree of metallurgical knowledge. Those castings were formed by the lost wax process, which later was modified and became known as investment casting. In various parts of India, this age-old casting process is still being practiced, without any major modifications. This paper discusses details of the process used by the Indian artisans of Swamimalai, Tamilnadu, and Mannar, Kerala, South India in shaping copper-base alloys into icons and utensils, bells, and lamps.
Indian artisans and craftsmen have long been masters at extracting and shaping metals and alloys, as proven by archaeological finds from the 2nd–3rd millennia B.C. For example, two well-known artifacts, castings of the dancing girl of Mohenjo Daro and the Mother Goddess of Adichanallur, Tamilnadu, depict a high degree of metallurgical knowledge. Those castings were formed by the lost wax process, which later was modified and became known as investment casting. In various parts of India, this age-old casting process is still being practiced, without any major modifications. This paper discusses details of the process used by the Indian artisans of Swamimalai, Tamilnadu, and Mannar, Kerala, South India in shaping copper-base alloys into icons and utensils, bells, and lamps.
INTRODUCTION
The history of metals and their shaping is as ancient as the history of civilization. Mastery of the mining, extraction, and working of metals was instrumental in the growth of the material culture. Many artifacts that have been excavated and preserved, as well as some of the metallurgical arts still being practiced, are examples of advanced, yet ancient, metallurgical skills. Historically, the Indian subcontinent was on par with the rest of the world in its metallurgical skill and expertise, and its artisans and craftsmen were masters at extracting and shaping metals. In fact, Indian knowledge of metallurgy predates technologies of many other civilizations, as shown by archaeological finds from the 2nd and 3rd millennia B.C.
Numerous ancient metallurgical arts and artifacts provide evidence of Indian excellence in the shaping of ferrous and nonferrous metals and alloys, including:
Numerous ancient metallurgical arts and artifacts provide evidence of Indian excellence in the shaping of ferrous and nonferrous metals and alloys, including:
|
In addition to these artifacts, during the reign of Alexander the Great, swords manufactured in the Middle East and Europe were made of steel imported from India. These metallurgical works were evidence of a high degree of technical excellence in shaping metals and alloys in general and copper-base alloys in particular as a single system.
Bronzes are copper-tin alloys. Those containing more than 11% tin have no engineering applications because of their increasing brittleness and, hence, decreasing ductility.1,2 However, high-tin bronzes containing 20–30% tin, also known as ß bronze or speculum or bell metal, have long been shaped and utilized as consumer articles such as mirrors, kitchen wares, musical instruments, bells, and ornaments in many parts of the world, including India.3–14 The peculiar properties of high-tin bronze—hard and brittle on slow cooling, ductile and malleable when worked at a particular temperature range, inert to the food native to Kerala (a southern province of India), and sonorous after hot working and quenching—had been identified and exploited by the Kerala artisans for shaping this material into metal mirrors (“aranmula kannadi” in Malayalam language),7–11 eating bowls (“Kadavaloor ottu kinnam” in Malayalam),9–13 and gongs (“kathakali chengala” in Malayalam). 9,11 Because the lost-wax process is still being used by the traditional metal workers in some areas of India, these metallurgical arts can be studied to gain insight into the science behind them. This article will review the authors’ studies of shaping bronze and other suitable copper-base alloys into icons, bells, lamps, etc. by the lost-wax technique in Swamimalai (Tamilnadu) and Mannar (Kerala), South India.
Bronzes are copper-tin alloys. Those containing more than 11% tin have no engineering applications because of their increasing brittleness and, hence, decreasing ductility.1,2 However, high-tin bronzes containing 20–30% tin, also known as ß bronze or speculum or bell metal, have long been shaped and utilized as consumer articles such as mirrors, kitchen wares, musical instruments, bells, and ornaments in many parts of the world, including India.3–14 The peculiar properties of high-tin bronze—hard and brittle on slow cooling, ductile and malleable when worked at a particular temperature range, inert to the food native to Kerala (a southern province of India), and sonorous after hot working and quenching—had been identified and exploited by the Kerala artisans for shaping this material into metal mirrors (“aranmula kannadi” in Malayalam language),7–11 eating bowls (“Kadavaloor ottu kinnam” in Malayalam),9–13 and gongs (“kathakali chengala” in Malayalam). 9,11 Because the lost-wax process is still being used by the traditional metal workers in some areas of India, these metallurgical arts can be studied to gain insight into the science behind them. This article will review the authors’ studies of shaping bronze and other suitable copper-base alloys into icons, bells, lamps, etc. by the lost-wax technique in Swamimalai (Tamilnadu) and Mannar (Kerala), South India.
ICON MAKING AT SWAMIMALAI, TAMILNADU
August Rodin, the famous sculptor, described the bronze icons of South India as “the most perfect representation of rhythmic movement in art.”12 These icons were and are still cast by Cire Perdue (cire and perdue meaning wax and lost, respectively). The lost-wax process11,14,15 became known as investment casting after a thorough modification and is now used for casting gas turbine blades, biomedical implants, etc. Lost wax has been the name used for all types of casting wherein a wax model forming the core of the image is drained out, then replaced by metal in the actual casting. This replacement can take place by two processes—solid casting (“ghana” in Sanskrit) and hollow casting (“sushira” in Sanskrit), both of which are referenced in the Rig Veda. Solid casting is still prevalent in South India (Swamimalai, Tiruchirapalli, Madurai, Chengleput, and Salem in Tamilnadu; Bangalore and Mysore in Karnataka; Mannar, Irinjalakuda in Kerala; and Tirupathi in Andhra), while the latter is largely prevalent in Central and Eastern India. The Silpasastra, an ancient Sanskrit text on icon making and the most elaborate treatise on the process believed to be compiled during Gupta period, set forth the composition and the preparation of the different alloys to be used, the measurements and the relative proportions of the different parts of icons, the method of preparing the wax model, and the making of the mold and the casting.
The unit of measurement in icon making is tala, which is the distance between the hairline and the end of the lower jaw. The tala is divided into 12 equal parts called angulas (equivalent to the breadth of a finger). Each angula is divided into eight yava (the size of a barley grain) and so on until the smallest unit, a paramu (smaller than the end of a single hair). The craftsmen use traditional tools, most of which are made by them. Of late, electrically operated tools such as drills, blowers, and files have been used. Icon making consists of the following four major steps:- Pattern/Model making: Pattern rule (Odiolai in the Tamil language) making, preparation of wax, and wax model making (Figure 1).
- Mold making: Mold making by investing (Figures 2 and 3), and melting and draining of wax from the mold cavity.
- Melting and casting: Preparation of alloy and casting.
- Fettling and finishing: Mold opening; finishing, engraving, and polishing; and coloring.
The unit of measurement in icon making is tala, which is the distance between the hairline and the end of the lower jaw. The tala is divided into 12 equal parts called angulas (equivalent to the breadth of a finger). Each angula is divided into eight yava (the size of a barley grain) and so on until the smallest unit, a paramu (smaller than the end of a single hair). The craftsmen use traditional tools, most of which are made by them. Of late, electrically operated tools such as drills, blowers, and files have been used. Icon making consists of the following four major steps:
Figure 1. A completed individual wax pattern/model of the child Krishna and a banyan tree leaf. | Figure 2. Completed mold halves with patterns after sun drying readied them for initiating preparation of other mold halves. | Figure 3. Completed molds for an icon of the child Krishna and banyan tree leaf. |
Initially, the artisan takes note of the proportion and measurements (i.e., talas) as laid down in Silpasastras for icon making and makes a pattern rule, which is a narrow ribbon of coconut tree leaf cut to the icon length requirement and folded at different lengths in proportion to the length of various parts of the icon. This means that the artisans make an individual pattern rule for a given size and shape of an icon.
Wax required for making the model or pattern of the icon is prepared by mixing pure bee’s wax, resin from the tree Damara Orientalis, and ground nut oil in the ratio 4:4:1. The powdered resin is mixed with ground nut oil and the mix is heated until a thick liquid forms. Next, bee’s wax is added to the thick liquid and stirred until it liquefies and gets well mixed. This wax melt is strained through a fine metal sieve or coarse-woven cloth into a container of cold water, thus allowing it to solidify. The wax mix is then used for wax model making.
Wax model making is a crucial step wherein the craftsman’s creativity decides the excellence of the model, and, in turn, of the icon to be cast. The head, body, and limbs of an icon are made separately by hand, using the wax mix after making it malleable by warming it and later shaping it using spatula, knife, and scraper. The finished parts of the icon are joined by using a hot iron tool as a soldering iron to melt their joining surfaces. The model or pattern for the icon’s pedestal is made as an integral part of the icon if the icon is small, or individually if the icon is large. To strengthen the wax pattern as well as to facilitate the flow of molten metal into various parts, a few wax cross strappings and a wax rod ending with a funnel shape (sprue and runner) are also joined to the pattern at appropriate locations. The wax pattern or model of the icon, with a gating system for metal flow, is now ready (Figure 1).
Mold making involves coating the wax pattern with layers of clay, known as investment—three layers for small icons and more layers for larger icons. A different clay is used for each layer. The first coat, about 3 mm thick, is made when fine loam or alluvial soil collected from the Cauvery river bed (called “vandal mann” in Tamil) is finely ground with charred paddy husk and mixed with cow dung, forming a thick mixture. This first coat performs two important functions: protection of the wax model and reproduction of the minute contours of the model. Thus, no portion of the wax model should be left uncovered except the wax sprue top surface, which is the outlet for the melted wax while dewaxing and the inlet for molten metal during casting. Further, no air bubbles should be allowed on the surface of this first coat, since they can spoil the mold cavity surface finish, and, in turn, that of the icon. During the clay-coating application, the wax model is kept on a piece of paper or cloth on the floor or a table, depending upon the size of the model, to avoid its deformation. The coating is applied to half the model, allowed to dry, and then the model is turned to coat the other half. It is crucial that the clay coating is dried either in mild sunlight or in the shade to prevent the wax model from melting.
The second coat or investment is made with a paste obtained by thoroughly mixing clay from paddy fields and sand, and combining that mixture with water in a 1:2 ratio. The thickness of this coat varies from 12.5–50 mm depending upon the size of the icon. The third coating is a paste containing a mix of coarse sand and clay. The mixture is applied after the second coating is dried. A fourth coat is applied only if necessary, based on the size of the icon. Especially with large icons, the mold must be reinforced with iron rods and wires to prevent the mold from giving way during handling and liquid metal pouring. When the last coat dries, one half of the mold is ready to withstand the pressure and heat of liquid metal. The same investment application procedure is repeated on the other half of the pattern, resulting in a completed mold with a wax model inside (Figure 3).
Next, the completed mold is heated in an open-ground oven using cow-dung cakes as fuel. The molten wax coming out through the runner is collected in a vessel containing water, and can be reused after any foreign matter is removed.
Silpasastras prescribe the composition of the alloy to be chosen for casting sacred icons. Archaeologists have excavated icons and idols proving that for the last 3,000 years, panchaloha (literally meaning an alloy of five metals) has been most widely used for making icons and idols. This five-metal combination of Cu, Au, Ag, Pb, and Zn was considered to be a highly auspicious composition and is still used for icons cast for worship. The important sources of information on making panchaloha are recorded in ancient Sanskrit and regional literature, with artisans from South India perfecting the technology. Other compositions of panchaloha cited include Au, Cu, Ag, Pb, Fe, and Sn as well as the combination of Sn, Cu, Fe, Pb, and brass.16 However, because of their high cost, gold and silver are no longer used in general-purpose icons. An alloy made by mixing copper, brass, and lead in the ratio 29:2:1 is commonly utilized for general-purpose icons. In some cases, tin is added in an amount equal to the lead content. Lead is added to make the alloy more malleable so that chiseling and engraving of the icon will be easy. The artisans believe that if the icon is made with copper alone, it will not have a lasting shine, whereas adding a little brass to copper results in a lasting shine and a lower melting point. It may be noted that brass is added as a master alloy to introduce zinc. The artisans calculate the weight of the alloy required to occupy the mold at eight times the weight of the wax model. Melting is carried out in a coke/charcoal-fired furnace using either a commercially available clay graphite crucible or a crucible made of clay by the artisans. When the alloy is being melted, the hollow mold is heated to red hot to drive away air bubbles from the inside of the mold cavity as well as to prevent sudden cooling of the molten metal, which could lead to an uneven surface finish. Heating the mold also prevents the mold from exploding because of the high heat of the liquid metal.
Wax required for making the model or pattern of the icon is prepared by mixing pure bee’s wax, resin from the tree Damara Orientalis, and ground nut oil in the ratio 4:4:1. The powdered resin is mixed with ground nut oil and the mix is heated until a thick liquid forms. Next, bee’s wax is added to the thick liquid and stirred until it liquefies and gets well mixed. This wax melt is strained through a fine metal sieve or coarse-woven cloth into a container of cold water, thus allowing it to solidify. The wax mix is then used for wax model making.
Wax model making is a crucial step wherein the craftsman’s creativity decides the excellence of the model, and, in turn, of the icon to be cast. The head, body, and limbs of an icon are made separately by hand, using the wax mix after making it malleable by warming it and later shaping it using spatula, knife, and scraper. The finished parts of the icon are joined by using a hot iron tool as a soldering iron to melt their joining surfaces. The model or pattern for the icon’s pedestal is made as an integral part of the icon if the icon is small, or individually if the icon is large. To strengthen the wax pattern as well as to facilitate the flow of molten metal into various parts, a few wax cross strappings and a wax rod ending with a funnel shape (sprue and runner) are also joined to the pattern at appropriate locations. The wax pattern or model of the icon, with a gating system for metal flow, is now ready (Figure 1).
Mold making involves coating the wax pattern with layers of clay, known as investment—three layers for small icons and more layers for larger icons. A different clay is used for each layer. The first coat, about 3 mm thick, is made when fine loam or alluvial soil collected from the Cauvery river bed (called “vandal mann” in Tamil) is finely ground with charred paddy husk and mixed with cow dung, forming a thick mixture. This first coat performs two important functions: protection of the wax model and reproduction of the minute contours of the model. Thus, no portion of the wax model should be left uncovered except the wax sprue top surface, which is the outlet for the melted wax while dewaxing and the inlet for molten metal during casting. Further, no air bubbles should be allowed on the surface of this first coat, since they can spoil the mold cavity surface finish, and, in turn, that of the icon. During the clay-coating application, the wax model is kept on a piece of paper or cloth on the floor or a table, depending upon the size of the model, to avoid its deformation. The coating is applied to half the model, allowed to dry, and then the model is turned to coat the other half. It is crucial that the clay coating is dried either in mild sunlight or in the shade to prevent the wax model from melting.
The second coat or investment is made with a paste obtained by thoroughly mixing clay from paddy fields and sand, and combining that mixture with water in a 1:2 ratio. The thickness of this coat varies from 12.5–50 mm depending upon the size of the icon. The third coating is a paste containing a mix of coarse sand and clay. The mixture is applied after the second coating is dried. A fourth coat is applied only if necessary, based on the size of the icon. Especially with large icons, the mold must be reinforced with iron rods and wires to prevent the mold from giving way during handling and liquid metal pouring. When the last coat dries, one half of the mold is ready to withstand the pressure and heat of liquid metal. The same investment application procedure is repeated on the other half of the pattern, resulting in a completed mold with a wax model inside (Figure 3).
Next, the completed mold is heated in an open-ground oven using cow-dung cakes as fuel. The molten wax coming out through the runner is collected in a vessel containing water, and can be reused after any foreign matter is removed.
Silpasastras prescribe the composition of the alloy to be chosen for casting sacred icons. Archaeologists have excavated icons and idols proving that for the last 3,000 years, panchaloha (literally meaning an alloy of five metals) has been most widely used for making icons and idols. This five-metal combination of Cu, Au, Ag, Pb, and Zn was considered to be a highly auspicious composition and is still used for icons cast for worship. The important sources of information on making panchaloha are recorded in ancient Sanskrit and regional literature, with artisans from South India perfecting the technology. Other compositions of panchaloha cited include Au, Cu, Ag, Pb, Fe, and Sn as well as the combination of Sn, Cu, Fe, Pb, and brass.16 However, because of their high cost, gold and silver are no longer used in general-purpose icons. An alloy made by mixing copper, brass, and lead in the ratio 29:2:1 is commonly utilized for general-purpose icons. In some cases, tin is added in an amount equal to the lead content. Lead is added to make the alloy more malleable so that chiseling and engraving of the icon will be easy. The artisans believe that if the icon is made with copper alone, it will not have a lasting shine, whereas adding a little brass to copper results in a lasting shine and a lower melting point. It may be noted that brass is added as a master alloy to introduce zinc. The artisans calculate the weight of the alloy required to occupy the mold at eight times the weight of the wax model. Melting is carried out in a coke/charcoal-fired furnace using either a commercially available clay graphite crucible or a crucible made of clay by the artisans. When the alloy is being melted, the hollow mold is heated to red hot to drive away air bubbles from the inside of the mold cavity as well as to prevent sudden cooling of the molten metal, which could lead to an uneven surface finish. Heating the mold also prevents the mold from exploding because of the high heat of the liquid metal.
Figure 4. Fettled castings of the child Krishna and a banyan tree leaf. | Figure 5. Finished icon of the child Krishna on a banyan tree leaf (Aal elai Krishnan in Tamil). |
When the temperatures of the metal and the mold have reached the levels required by the artisan for casting, the red-hot mold is firmly placed or buried in the ground so that only the sprue portion protrudes out. A cloth-wound metal ring is placed on the sprue top to support the hot crucible containing molten metal as well as to prevent overflow of the metal as it is poured into the mold. Care is also exercised that the metal stream does not cover more than half of the sprue opening to allow displaced air to escape from the mold cavity. In order to prevent the entry of any impurities floating on the surface of the molten metal, a piece of knitted jute cloth is used to cover the mouth of the crucible while pouring. The filled mold is allowed to cool slowly, which normally takes a day or more depending on the size of the icon. However, if immediate cooling is necessary, it can be doused with water after 2–3 hours of casting.
The breaking of the mold to remove the icon is of great significance to the craftsman, since it is not merely an object but a transcendental entity. The fettling of the casting or breaking of the mold is initiated only when the mold has sufficiently cooled. The mold portion holding the icon head is always broken first followed by remaining portions. The iron rods and wires used as reinforcements are separated and preserved for reuse. The clay sticking to the icon is scrapped and then the connecting rods used as support in complicated icons are removed by chiseling. The fettled castings of the child Krishna and a banyan tree leaf are shown in Figure 4. The contours and details of the original wax pattern are recaptured by smoothing the uneven surfaces and then by chiseling. The details of dress and ornaments as well as other final touches are engraved into the icon. The icon surface is smoothed by rubbing it with fine-grade emery paper, and then it is cleaned with tamarind and a soap-nut-water mix and scrubbed with a wire brush. Finally, the piece is brushed with polishing sand and water. The well-finished icon is shown in Figure 5 after the two individually cast parts have been riveted.
The icon of the child Krishna on a banyan tree leaf (Aal elai krishna in Tamil) was made by Swamimalai artisans. Generally, they use 80% copper, 20% brass, and 5% lead for general-purpose icons. However, for icons to be installed in temples for worship, panchaloha containing 50% Cu, 16% Au, 8% Ag, 10% brass, and 16% Pb is used.
The breaking of the mold to remove the icon is of great significance to the craftsman, since it is not merely an object but a transcendental entity. The fettling of the casting or breaking of the mold is initiated only when the mold has sufficiently cooled. The mold portion holding the icon head is always broken first followed by remaining portions. The iron rods and wires used as reinforcements are separated and preserved for reuse. The clay sticking to the icon is scrapped and then the connecting rods used as support in complicated icons are removed by chiseling. The fettled castings of the child Krishna and a banyan tree leaf are shown in Figure 4. The contours and details of the original wax pattern are recaptured by smoothing the uneven surfaces and then by chiseling. The details of dress and ornaments as well as other final touches are engraved into the icon. The icon surface is smoothed by rubbing it with fine-grade emery paper, and then it is cleaned with tamarind and a soap-nut-water mix and scrubbed with a wire brush. Finally, the piece is brushed with polishing sand and water. The well-finished icon is shown in Figure 5 after the two individually cast parts have been riveted.
The icon of the child Krishna on a banyan tree leaf (Aal elai krishna in Tamil) was made by Swamimalai artisans. Generally, they use 80% copper, 20% brass, and 5% lead for general-purpose icons. However, for icons to be installed in temples for worship, panchaloha containing 50% Cu, 16% Au, 8% Ag, 10% brass, and 16% Pb is used.
MAKING VESSELS, LAMPS, AND BELLS AT MANNAR, KERALA
The process followed at Mannar for making vessels, lamps, and bells is similar to that followed in Swamimalai for icon making. However, in the Mannar process, one half of the mold is made first over which the required thickness of wax is deposited, then the other half of the mold is made covering the wax pattern. The important steps involved in making a vessel (urli in Malayalam language) are shown in Figures 6, 7, 8, 9, 10, 11, 12, and 13 and those for making a bell are depicted in Figures 14, 15, and16. These craftsman still follow the old method of using broken earthenware pieces as reinforcement in making utensils and bells (Figure 11). Brass and bronze are used for making utensils, and bronze (Cu-20%Sn) alone is utilized for making bells.
Figure 6. A portion of the mold built over the disc made out of a mixture of clay, wellground broken mold powder, and jute fiber. | Figure 7. Turning the mold using a sharp tool to make it concentric by rotating the same by hand. |
| ||||
Figure 10. A mold portion with a fine powder mix layer and wax layer over it. | Figure 11: A finished mold for a vessel with broken earthenware pieces as reinforcements and the sprue for metal entry at the center. | Figure 12. The dewaxing of three utensil molds by heating them in coconut shells and collecting the molten wax in a vessel containing water. |
![]() | ||||
Figure 13. Finished vessels of different sizes and shapes. | Figure 14. Making one half of bell mold. | |||
![]() | ||||
Figure 15. A bell mold with smoothed wax layer over which the other mold half is to be completed. | Figure 16. Fettled bells of two different sizes. | |||
ACKNOWLEDGEMENTS
The authors gratefully acknowledge the valuable cooperation of Shri. Karunanithi Sthapathi and Shri. Sivan Asari, the master craftsmen, and their colleagues for this study on Swamimalai icons and Mannar utensils and bells, respectively. The authors thank the Director, Regional Research Laboratory, Thiruvananthapuram for granting permission to publish this paper, and P. Vijaya Kumar for photography.References1. E.G. West, Copper and Its Alloys (New York: Ellis Horward Ltd., John Wiley and Sons, 1982), pp. 106–110.
2. Metals Handbook, vol. 2, 9th ed. (Materials Park, OH: American Society of Materials, 1979), p. 418.
3. J.E. Hughes, Metals and Materials (May/June 1981), pp. 51–58.
4. McGraw Hill Encyclopedia of Science and Technology, vol. 2 (1997), pp. 379–380.
5. Martha Goodway, Journal of Metals, 40 (3) (1988), pp. 36–37.
6. Martha Goodway, Journal of Metals, 40 (4) (1988), pp. 62–63.
7. S.G.K. Pillai, R.M. Pillai, and A.D. Damodaran, JOM, 44 (3) (1992), pp. 38–40.
8. The Hindu Weekly Magazine Edn., 3 (17 April 1994), IX.
9. R.M. Pillai, S.G.K. Pillai, and A.D. Damodaran, Metals, Materials and Processes, 13 (2–4)(2001) 291–300.
10. R.M. Pillai, A.D. Damodaran, and S.G.K. Pillai, Trans. IIM ( in press).
11. Sharada Srinivasan, JOM, 50 (7) (1998), pp. 44–47, 49–50.
12. S.G.K. Pillai et al., JOM, 46 (3) (1994), pp. 59–40.
13. R.M. Pillai, S.G.K. Pillai, and A.D. Damodaran, Practical Metallography, 32 (9) (1995), pp. 478–482.
14. Metal Craft (Bangalore: Pubr. Crafts Council of India, 1993).
15. C. Sivaramamurti, South Indian Bronzes (Madras: Lalit Kala Academy, 1981).
16. N. Gopalakrishnan, Ancient Indian Knowledge in Metals and Alloys Heritage Publications, Series 38 (Thiruvananthapuram, India: Indian Institute of Scientific Heritage, 2001), pp. 20–21.For more information, contact R.M. Pillai, Regional Research Laboratory, Council of Scientific & Industrial Research, Thiruvananthapuram – 695019, India; e-mail rmpillai@csrrltrd.ren.nic.in or rmpillai12@rediffmail.com.
2. Metals Handbook, vol. 2, 9th ed. (Materials Park, OH: American Society of Materials, 1979), p. 418.
3. J.E. Hughes, Metals and Materials (May/June 1981), pp. 51–58.
4. McGraw Hill Encyclopedia of Science and Technology, vol. 2 (1997), pp. 379–380.
5. Martha Goodway, Journal of Metals, 40 (3) (1988), pp. 36–37.
6. Martha Goodway, Journal of Metals, 40 (4) (1988), pp. 62–63.
7. S.G.K. Pillai, R.M. Pillai, and A.D. Damodaran, JOM, 44 (3) (1992), pp. 38–40.
8. The Hindu Weekly Magazine Edn., 3 (17 April 1994), IX.
9. R.M. Pillai, S.G.K. Pillai, and A.D. Damodaran, Metals, Materials and Processes, 13 (2–4)(2001) 291–300.
10. R.M. Pillai, A.D. Damodaran, and S.G.K. Pillai, Trans. IIM ( in press).
11. Sharada Srinivasan, JOM, 50 (7) (1998), pp. 44–47, 49–50.
12. S.G.K. Pillai et al., JOM, 46 (3) (1994), pp. 59–40.
13. R.M. Pillai, S.G.K. Pillai, and A.D. Damodaran, Practical Metallography, 32 (9) (1995), pp. 478–482.
14. Metal Craft (Bangalore: Pubr. Crafts Council of India, 1993).
15. C. Sivaramamurti, South Indian Bronzes (Madras: Lalit Kala Academy, 1981).
16. N. Gopalakrishnan, Ancient Indian Knowledge in Metals and Alloys Heritage Publications, Series 38 (Thiruvananthapuram, India: Indian Institute of Scientific Heritage, 2001), pp. 20–21.